(PDF) Sustainable Use of Copper Resources: …
Sustainable Use of Copper Resources: Beneficiation of Low-Grade Copper Ores. April 2022. Minerals 12 (5) DOI: 10.3390/min12050545. License. CC BY 4.0. Authors: Silpa Sweta Jena. …
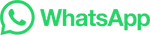
Sustainable Use of Copper Resources: Beneficiation of Low-Grade Copper Ores. April 2022. Minerals 12 (5) DOI: 10.3390/min12050545. License. CC BY 4.0. Authors: Silpa Sweta Jena. …
The processing technology of copper ore beneficiation plants includes flotation, microbial leaching, segregation, beneficiation, etc. Single sulfide ore is mostly processed by flotation, and copper ore …
Acid leaching; 3. Copper ore plant advantages. Dasen Mining has been specialized in copper flotation research for more than 20 years. Whether it is copper oxide or copper sulfide, our company's professional technical team will give the best beneficiation plan based on specific mineral indicators and experimental results.
copper Processing Plant. 1. Copper flotation process. The setup is complete copper flotation plant; main equipment and process details as follows: 1. Crushing: Adopts two-stage open-circuit crushing and selects jaw crusher for crushing, and the crushed product is transported to fine jaw crusher for two-stage crushing. 2.
A Pure copper sample (malachite and azurite) from the Dishui Copper Processing Plant of China was used in the flotation experiments. These researchers concluded a possible better recovery of …
In many lithium ore beneficiation plants, it is a common practice to de-slime the ore prior to flotation. De-sliming is typically carried out to remove the −20 µm size fraction to improve selectivity of separation because slimes are detrimental to the flotation circuit (Bale and May, 1989). As is the case in many operations, de-sliming is ...
Copper ore beneficiation process and production processes mainly include three processes: crushing, grinding, and beneficiation. The cost of processing mixed minerals is higher. Magnetic properties, impurities and rock need to be extracted. For higher benefication effects, flotation machine and suitable chemical reagents need to be used.
Fig 1 Typical flow-sheet of ore beneficiation plant. Several methods / techniques such as washing, jigging, magnetic separation, gravity separation, and flotation etc. are used to improve the Fe content …
Copper ore beneficiation process is based on the physical and chemical properties of different minerals in copper ore. After the ore is crushed and ground, gravity separation, flotation, magnetic separation, electric separation and other ore …
1. Copper Flotation. As a commonly used process for copper ore beneficiation, flotation can be used for the separation of copper sulfide and oxidized copper ores. The main …
To a large extent, phosphate beneficiation plants are in areas where there is limited water or brackish hard water. A key development to come out of this predicament is the drive towards using saline/hard water in wet beneficiation with quality water (potable water) used to rinse the chlorides from the final phosphate concentrate. ...
The processing technology of copper ore beneficiation plants includes flotation, microbial leaching, segregation, beneficiation, etc. Single sulfide ore is mostly processed by flotation, and copper ore processing equipment adopts the crushing-grinding-classification-flotation-concentration process to select single copper sulfide ore as …
It can also be used to study flotation of different types of ores. A picture of the pilot scale beneficiation plant is shown in Fig. 1. Currently the raw material used in the mini-pilot plant is sulphide ore mined from the Pyhäsalmi deposit in central Finland. The main minerals of the ore are chalcopyrite, pyrite, sphalerite, galena and quartz.
In Las Luces beneficiation plant, NaHS is employed to depress the floatability of copper ores in the copper-molybdenum ores (Cu-Mo) flotation using seawater (Moreno et al., 2011). These inorganic ...
The copper ore beneficiation plant uses three processes: crushing, grinding and beneficiation. It's just that the selection of individual copper ore processing equipment and beneficiation technology will be slightly different. Among them, in the crushing process, the use of three-stage closed-circuit crushing can well complete the work of ore ...
The difficulty mainly comes from the lack of daily records for the slag discharged, the variability of ore, raw material, the process used from one plant to another, and the slag-to-metal production ratios. For example, for copper production, the ratio of slag to metal is in the range of 0.6:1 to 1.5:1 (Kokal, 2006). For lead production, the ...
Copper Production. W.G. Davenport, in Encyclopedia of Materials: Science and Technology, 2001 1.1 Physical Beneficiation. Beneficiation of copper ores is done almost exclusively by selective froth flotation. Flotation entails first attaching fine copper mineral particles to bubbles rising through an ore–water pulp and, second, collecting the copper …
The dominant challenge of current copper beneficiation plants is the low recoverability of oxide copper-bearing minerals associated with sulfide type ones. Furthermore, applying commonly used ...
The Las Cenizas ores are treated in the Las Luces beneficiation plant, located 45 km South East from Taltal. This plant comprises crushing, milling and flotation unit operations. A variety of ores is supplied to the Las Luces beneficiation plant from the neighbouring Las Cenizas mines at a rate of 60,000 metric tonnes/month. Ore grades …
In iron ore beneficiation plants, the spiral concentration technique is being used to obtain a fine concentrate. In spiral separators, the separation of heavy and light minerals takes place in streaming currents. The equilibrium between the centrifugal force outwards and the gravitational force downwards facilitates the separation of particles ...
There are many reasonable beneficiation methods for extracting associated minerals from copper ores. It usually also includes crushing, grinding, gravity separation …
1.0 Introduction. 1.1 Mineral Processing and Extractive Metallurgy. Mineral processing is a major division in the science of Extractive Metallurgy. Extractive metallurgy has been defined as the …
Multotec is a specialist in copper mineral processing equipment, with over 50 years of experience in mineral processing across the world. Our Research and Development (R&D) department responds to our customers' unique processing challenges, creating innovative solutions through new beneficiation technologies.
Process mineralogy is the applied science subject that investigates the chemical composition, mineral composition, and mineral characteristics and changes of raw ore materials and ore processing products. It is a subject developed from mineralogy and mineral processing, and plays an important role in identifying the proper beneficiation …
Ore processing flow: 1 Crushing: Use stone crushers to crush the copper ore to 0–5 mm or 0–9 mm. 2 Washing: Use a spiral classifier to wash away the clay and screen out copper ore with a qualified particle size. 3 Grinding: The electromagnetic feeder sends the copper ore with qualified particle size to the ball mill for grinding.
[18] concludes that the projects of new operating plants for the beneficiation of copper-bearing ores mainly use the HPGR technology (for hard ores) and SAG mills (for ores with medium and soft ...
Contribute to jgw2023/sbm development by creating an account on GitHub.
A heavy media plant will be used to beneficiate ore mined underground. COPPER: The major development in Michigan's copper industry during 1953 was the materialization of the White Pine Copper Company's venture in Ontonagon County. A complete new townsite, as well as mill, smelter, and other plant facilities were under construction and
The main methods of processing copper oxide ore are: Flotation and Leaching. For copper oxide ore with large mud content and easy to mud, the traditional sulfidation flotation recovery rate is low, and it is difficult to solve the problem of mud interference; the stirred leaching method has the advantages of short leaching cycle and high copper leaching …
Hindustan Copper Limited (HCL), a public sector undertaking under the administrative control of the Ministry of Mines, was incorporated on 9th November 1967. It has the distinction of being the nation's only vertically integrated copper producing company as it manufactures copper right from the stage of mining to beneficiation, smelting, refining …
حقوق النشر © 2024.Artom كل الحقوق محفوظة.خريطة الموقع