Separating Success – Royal White Cement
For the separation of mill discharge material and cement separation via high efficiency cyclones or process filters. ICD vertical air separator with an installation …
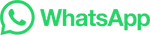
For the separation of mill discharge material and cement separation via high efficiency cyclones or process filters. ICD vertical air separator with an installation …
Our ATOX® Coal Mill is a compact vertical roller mill that can grind almost any type of raw coal. The coal mill utilises compression and shear force generated between the large rollers and the rotating table to crush and grind raw coal, removing the need for a separate piece of equipment for crushing. The coal mill can also grind petroleum ...
Separators in the cement industry. relatively large particles from gas streams. Static separators are relatively inexpensive since they have no moving parts and they are easy …
Optimum performance of ball mill could potentially refine Blaine fineness, thereby improving the cement quality. This study investigates the effects of separator speed and mill speed on Blaine ...
Electrostatic precipitator ( ESP ), also known as high voltage electrostatic precipitator, electrostatic dust collector, is a dust collector using electric power. It is one of the commonly used environmental protection equipment for dust gas purification. It is widely used in electric power, metallurgy, building materials, chemical industry ...
Cement Manufacturing Equipment. Electrostatic Precipitator. Product Name: Electrostatic precipitator / ESP in cement plants. Dust Collecting Rate: ≥99.5. Weight: 4500 ~ 6900 kg. Equipment Resistance: ﹤ 400 Pa. Air Volume: 2460 ~ 11000 m 3 /h. Condition: Brand new. SEND INQUIRY.
Adjusting mill parameters: Fine-tuning mill parameters such as mill speed, ball charge, filling ratio, and grinding media size can have a substantial impact on the grinding efficiency of the mill. For example, a 10% increase in mill speed can result in up to 10% higher production rate, while optimizing the ball charge can lead to a 5-10% ...
China O-Sepa cement mill separator supplier offers O-Sepa cement mill separator, max capacity 180-300 T/H, air volume 500-5000 M3/H, max feeding 75-... O-SEPA - PS-01 - Cement Plant Machinery - Powder Separator - Cement Mill Separator By Sinospare - Xiamen Linse Eastern Import & Export Co., Ltd.
Abstract. An improved differential evolutionary cement mill operation index decision algorithm based on constraint control and selection strategy is proposed to address the problem that the operation index is usually decided by manual experience in the cement mill operation process, which causes unqualified cement specific surface area and …
4.0 AIR SEPARATORS. 4.1 Introduction. Separators are utilized in a closed circuit grinding system for the purpose of separating (classifying) the fine and coarse particles of the feed. The fine particles are passed through the separator to become finished product while the coarse particles are returned to the mill as rejects for further grinding.
Monitoring and control of burning and cooling systems. Kiln inlet gas analysis Control of raw material input volume Kiln rotation speed control and load balance control Kiln monitoring Kiln hood draft control Tertiary airfl ow control Preheater induction draft fan (IDF) damper control. 【System confi guration】. Raw material processes.
The separator for better quality and economy. The Pfeiffer separators have undergone optimization for years by means of CFD simulation on the basis of small-scale investigations and last but not least by making use of our …
Several types of grinding media are used in cement mills, including: 1. Steel Balls. Steel balls are the most widely used grinding media in cement mills. They are made from carbon steel and are available in various diameters. Steel balls are used to crush and grind the raw material in the cement mill. 2.
The Raymond ® Mechanical Air Separator produces material with high uniform fineness; operates in open or closed circuit; can provide drying and cooling; is excellent for de-dusting and features the unique single or double whizzer for faster separation of fines and more positive rejection of oversize. Single whizzer separators have only one row ...
Finish mill – 12. Cement – 13. Quality control – 14. Packing and distribution – 15. Emission abatement (dust, NO x, SO 2, etc) – 16. Maintenance – 17. Process – 18. Materials analysis –19. Plant capacity summary – 20. Storage capacity 15. Cement plant construction and valuation 244 1. New plant construction – 2.
The coarse particles exit from the bottom of the separator and by an air slide, are recycled into the cement ball mill. A mixture of air and fine particles are directed to the cyclone separators for complete separation of cement particles, this fine powder should have a specific surface area around 3000 cm 2 /g (Ghalandari & Iranmanesh, 2020).
Separators - Cement Plant Equipments Cement Plant Separator Manufacturers The separators are known to be widely deployed in cement manufacturing industry especially in the field of grinding circuits. The basic function of these separators is to separate very fine sized particles from the coarse particles. During the separation process, the …
The OK Mill combines the drying, grinding, material conveying and separation processes into one compact unit, requiring fewer machines in the mill circuit and therefore, simplifying plant layout. ... Sharing of common parts is possible across different vertical roller mill sizes for both cement and raw applications. This offers you more ...
In this paper, chaos theory principle is applied in studying the concrete mixing process. Using piecewise linear mapping model describes the stirred mixture mixing and separation process.
In this chapter an introduction of widely applied energy-efficient grinding technologies in cement grinding and description of the operating principles of the related equipments and comparisons over …
Highlights. •. Direct separation reactors (DSR) could capture 58–68% of direct emissions, reducing net CO 2 to 0.17–0.21 t CO2 /t cement. •. This could be …
Cement Mill Separator is a cyclone separator that separates fine powder and coarse particles in cement clinker through centrifugal force and gravity. It is usually installed at …
Separators in the cement industry. relatively large particles from gas streams. Static separators are relatively inexpensive since they have no moving parts and they are easy to operate. The material enters with the …
High Efficiency Separation System - O-SEPA®. O-SEPA® is a high efficiency air separator which has been developed aiming at energy saving and quality improvement in cement grinding system. More than 660 …
As the amount of available space in the former mill building of cement mill 2 was very limited, great precision was required in both the planning and the execution stages. The structural planning by Ingenieurbüro Kranz envisaged a completely new interior steel construction for accommodating the new separator. This was built by Messrs. Hoffmeier.
The vertical roller mill (VRM) is a type of grinding machine for raw material processing and cement grinding in the cement manufacturing process.In recent years, the VRM cement mill has been equipped in more and more cement plants around the world because of its features like high energy efficiency, low pollutant generation, small floor area, etc.. The …
KILN GAS is often used for the raw mill instead of the cement mill because the temperatures are higher than cooler air (typically 300 –350°C) and the raw meal is generally more moist than cement. ... Enhances flowability, …
Compared to conventional cement mill separators, our cyclone air separators have the following advantages: Separate the material into three parts: coarse powders …
F.L. has developed this cement grinding system which is a fully air-swept ring roller mill with internal conveying and grit separation. This mill is a major improvement of the cement grinding systems known today which are ball mill, roller press (HPGR)/ball mill, vertical roller mill and closed-circuit roller press for finish grinding.
Steel balls are one of the most widely used grinding media in cement ball mills, their diameters can range from 20mm to 120mm according to different grinding requirements. In a cement ball mill, generally, φ50–100mm steel balls are used in the coarse grinding chamber, φ20–50mm steel balls are used in the fine grinding chamber. 2.
حقوق النشر © 2024.Artom كل الحقوق محفوظة.خريطة الموقع