Mastering the Art of Micro-Grinding | Custom Wire …
Micro-grinding is a tool-based machining process that creates micro-features on hard, brittle materials. It uses a large tool to create minute details, which makes it an extremely important …
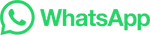
Micro-grinding is a tool-based machining process that creates micro-features on hard, brittle materials. It uses a large tool to create minute details, which makes it an extremely important …
Micro-grinding is a tool based mechanical micromachining process which is mostly applied to create and finish 3D micro-features on hard and brittle …
Micro grinding is a promising process to produce small scale structures in hard and brittle materials. Just like macro grinding processes, a high number of abrasive grits embedded on the grinding … Expand. 8. Save. Micromachining of Silicon - Study on the Material Removal Mechanism.
Deburring Definition. Deburring is the process of removing the small imperfections known as burrs from machined metal products. Machining processes shape a piece of metal in different ways. Stamping, for instance, presses the workpiece in a die set, while milling uses a rotating tool to shave metal off a workpiece.
Micro-grinding. Micro-grinding is a process that helps create and finish 3D micro-features. It uses miniature-sized tools with abrasives like cubic boron nitride (CBN) or diamond to remove unwanted material from both hard and brittle workpieces made of aluminum, silicon, and glass. These tools generally have a diameter of less than 1 mm — …
Blanchard grinding is a term which through common usage in the manufacturing industry has come to be recognized throughout the world as identifying the most efficient method of finishing flat surface on virtually any material. The finish is produced by utilizing a vertical grinding spindle with a cylindrical grinding wheel and, generally, a ...
Grinding process is a micro-processing method. Grinding uses a grinding tools and abrasive (a free abrasive) to generate relative movement between the processed surface …
Mechanical and thermal effects in grinding of advanced ceramics. H. Tönshoff T. Friemuth D. Hessel T. Lierse. Materials Science, Engineering. 1999. 3. Semantic Scholar extracted view of "Potentials of Different Process Kinematics in Micro Grinding" by B. Denkena et al.
In this study, we review the basic mechanism of micro-grinding, the development of micro-grinding tools, micro-grinding of different materials, effect of …
Summary. This chapter presents an overview of the micro grinding technologies developed for hard and brittle materials. It summarizes the principle and …
Superb grinding machines now produce optical quality finishes due to developments in process control and machine design. It is the same for extremely high removal rates.
This paper investigates the characteristics of a nanofluid MQL micro-grinding process through a series of experiments. The miniaturized desktop machine tool system is developed, and a small grinding wheel is used to effectively realize the nanofluid MQL microgrinding process. Nanodiamond and nano-Al2O3 particles are selected, and …
Micro machining, a term synonymous with precision and ultra-fine detail, refers to a manufacturing process where material is removed from a workpiece on a micrometer scale. This technique is pivotal in producing micro components with high …
The "micro-grinding head" formed by the magnetorheological fluids with polishing abrasives, entrains the abrasives in the polishing fluid and holds the ones at the surface interface in relative motion and under pressure to affect the polishing action. ... The laser micro-polishing process using continuous and pulsed modes is described. Li ...
The Glebar TF-9BHD Infeed/Throughfeed Centerless Grinder is a manual system capable of grinding both hard and soft materials including catheters, medical guidewires, and spinal cord stimulators. Glebar's Micro Grinding Machines can grind parts from semiconductor probe pins to medical components like guidewires, bone pins, screws, mandrels ...
Micro-milling represents an attractive alternative to conventional milling under the right circumstances, and is a fresh approach to surface preparation and increasingly surface rehabilitation. Because this process is relatively new, the long-term performance of micro-milling solutions lacks a wealth of data and experience.
The basic purpose of grinding coffee beans is to facilitate the extraction process by exposing more surface area to the hot water. Basically, the process of making coffee happens as roasted coffee beans are brought into contact with hot water that 'extracts' the flavour, ideally resulting in a delicious cup of brew.
Micro-milling is a precision manufacturing process with broad applications across the biomedical, electronics, aerospace, and aeronautical industries owing to its versatility, capability, economy, and efficiency in a wide range of materials. In particular, the micro-milling process is highly suitable for very precise and accurate machining of mold …
In micro-grinding process, the rounded corner radius of abrasive particles have significant influence on the grinding force, which differs from the traditional grinding process [31]. Therefore, the flat bottom parabolic head in contact mechanics [32] is used to establish the simulation abrasive particle.
Grinding Process Grinding is a surface finishing operation where very thin layer of material is removed in the form of dust particles. Thickness of material removed is in range of 0.25 to 0.50 mm. Tool used is a abrasive wheel Grinding machine is a power operated machine tool where, the work piece is fed
Improving the optical properties of the optical materials by using ceramic-based grinding wheel and centerless grinding process is one of the practical engineering methods to solve the issues of microdiameter precision grinding of YAG (Y 3 Al 5 O 12) optical crystal materials.YAG is a new substrate and UV and infrared optical window …
Microfinishing (superfinishing) is the ultimate abrasive process, allowing users to: Remove the amorphous surface layer (thermally damaged) caused by grinding. Obtain very consistent surface finishes with predictable and repeatable results. Achieve virtually any surface finish - Ra, Rz, Rt, Rpk, Bearing Area. Eliminate microscopic burrs left by ...
Grinding process can achieve minimal material removal quantity and multiple material removal mechanisms simultaneously, which makes it extremely popular in industrial applications to meet the requirements of high dimension precision, excellent surface quality and rigorous tolerance. ... On the other hand, the micro grinding …
Grinding is a metal-cutting operation, so grinding is a subset of cutting. The cement industry and mineral processing facilities grind frequently. Workpieces that need high surface quality and accuracy in shape and dimension are finished with grinding. Grinding can be used in roughing applications to remove large amounts of metal quickly.
With the in-feed method, the regulating wheel spins the part at one speed while pushing it towards the grinding wheel, which is spinning at a faster speed. The greater the difference in speeds, the faster the removal rate. 4. The choice of grinding wheel is critical. Another key factor in centerless grinding is the choice of grinding wheel.
Generally speaking, if a normal microdose is 0.1 – 0.3 grams of mushrooms, you'll want to start with 0.1 grams if your body weight is below 100 lbs. However, if you weigh about 200 lbs, you may be comfortable starting with 0.3 grams. Double these starting doses for truffles. Here is a useful dosage calculator.
In micro-grinding process, the diameter of the tool is small, and the free length is normally large. This means that the micro-tools are comparatively weaker than the macro-tools. Thus, they can easily be deflected during the process. As a result, the actual material removal deviates from the nominal depth of cut which directly influences the ...
The micro-grinding process of DD5 material using MGTP can be illustrated as Fig. 6, and the grit shape can significantly affect micro-grinding process . In rubbing stage ( l e ), the elastic and local plastic deformation are dominated by elastic force occurring on the workpiece, and some large size abrasive particles exceed strength limit …
The peak and the valley of micro-dimples are over 5 μm and 10 μm, respectively, and the largest width of pits is over 10 μm (Fig. 10 e~ 10 f). This is mainly due to the impact of steel balls and the micro-cutting of grinding powder. As the coverage increases to 300 %,the peaks and valleys of micro-pits get lower.
Electrochemical grinding is a process that removes electrically conductive material by grinding with a negatively charged abrasive grinding wheel, an electrolyte fluid, and a positively charged workpiece. Materials removed from the workpiece stay in the electrolyte fluid. Electrochemical grinding is similar to electrochemical machining but …
حقوق النشر © 2024.Artom كل الحقوق محفوظة.خريطة الموقع