Pulverizer Plant O&M Aspects
Nomenclature-Bowl Mills 583 XRS / 803 XRP Bowl mills 58,80 stands for bowl diameter in inches If the number is even then its shallow bowl mill. If the number is odd then its deep bowl mill 3 - number of rollers three nos. X - frequency of power supply 50 cycles.In USA 'x' means 60 cycles. R- Raymond, name of the inventor
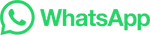