Overview of cement grinding: fundamentals, …
Grinding Aids reduce particle re-agglomeration during and after the milling process so improving the yield. Strength enhancers push clinker reactivity increasing the use of SCM in blended...
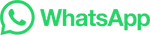
Grinding Aids reduce particle re-agglomeration during and after the milling process so improving the yield. Strength enhancers push clinker reactivity increasing the use of SCM in blended...
2. Background. AAMs are synthesized by the reaction of an aluminosilicate-based precursor (xSiO 2 ∙ yAl 2 O 3), alkali activators (MOH and M 2 SiO 3; where M is either alkali ion Na + or K +) and water (H 2 O). No Portland cement is required to produce alkali-activated binders, but AAMs could also be added as a supplementary cementitious …
The grinding process involves reducing the clinker particles to a specific fineness, typically measured in terms of Blaine specific surface area or particle size distribution. The grinding process significantly influences the cement's strength development, setting time, and other performance characteristics.
SPL materials can be co-processed successfully in cement industries as alternative raw materials for cement production. SPL is believed to contribute in reducing NOx emissions from cement production mainly through two ways; 1) The SPL materials help reduce the kiln temperature, or melting point of cement raw mix thus reducing the …
Adding 5% limestone would reduce fuel consumption by 5% (or on average 0.35 GJ/t clinker), power consumption for grinding by 3.3 kWh/t cement, and CO2 emissions by almost 5%. Additional costs would be minimal, limited to material storage and distribution, while reducing kiln operation costs by 5%. Low-Alkali Cement.
Grinding down concrete is a fairly straightforward process. Most of the time, grinding down concrete slabs can be done with a handheld angle grinder and an attached diamond cup wheel. If grinding is needed in large quantities, it can be done with walk-behind grinding units. To go about doing the actual grinding with a handheld grinder, …
The current global consumption of cement industry is about 1.5 billion tons per annum and is rising at almost 1% per annum. Cement production requires approximately 110 kW h/t of electrical energy, with 40% directed to clinker grinding [26].Using real auditing, Avami and Sattari [17] investigated technological methods that …
There are so many advantages of using grinding aids. For example, these are greater specific surface area, improved cement granulometry, lower grinding media consumption, higher separator ...
The cement industry will have to gear up to meet fresh challenges in the future, such as upgrading its technologies for carbon capture and storage, says SAILESH MOHTA, PRESIDENT – MARKETING, WONDER CEMENT. India is the second-largest cement producer in the world and accounts for 6.7 per cent of the world's cement output.
Add to Mendeley. Share. Cite. ... The cement manufacturing process involves three key steps, including preparing and grinding the raw materials, heating the newly formed clinker in a kiln, and final production of cement through grinding. ... Chinese cement industry released about 1094 Mt CO 2 e in 2009, accounting for 3.56% of the …
Step 5: Cement grinding After mixing with gypsum and admixtures, the clinker is sent to a cement mill for grinding. Cement grinding can be carried out either in an integrated cement plant or in a stand-alone cement grinding station. 3. What should limestone be mixed with to make cement? This needs to start with the cement …
However, as shown in Fig. 1, due to the huge capacity gap between the steel industry and the cement industry, the supply of GBFS is far from meeting the demand of the cement industry and some countries even rely on imported GBFS to meet their demands.In addition, the price of S95 GBFS used in the cement and concrete industry …
Over the years technology in the cement industry has developed with a growing focus on sustainable and also cost and energy efficient production. While significant steps may not seem visible on a year to year basis, the medium-term view shows notable progress. The drivers for progress are certainly cost-based, but at the same time the …
The cement factory where the measurements were made was located in Romania's center-north and had a final section with two cement mills. Cement grinding was performed inside the cement mill workshop. This manufacturing phase's product was cement—a powdery, finely ground material in closed-loop tubular ball mills (Figure 1). …
Since the cement industry acts as a significant contributor to carbon emissions in China, China's national emission trading system has announced that it should be included in the system soon. However, current cement carbon accounting methods require high-resolution data from various processes on the production line, making it a …
Nearly 32% of India's cement production capacity is based in South India, 20% in North India, 13% in Central, 15% in West India, and the remaining 20% is based in East India. India's cement production reached 374.55 million tonnes in FY23, a growth rate of 6.83% year-on-year (yoy). Between FY12 and FY23, the installed capacity grew by 61% to ...
1.. IntroductionChina is the largest cement producing and consuming country in the world. Cement production in China was 1.39 billion metric tons in 2008 (CMIIT, 2009), which accounted for 50% of the world's production (USGS, 2009).Enormous quantities of air pollutants are emitted from cement production, including SO 2, NO X, CO, and PM, and …
Add to Mendeley. Share. Cite. https: ... The Indian cement industry is not far behind with a 9% contribution to national emission inventory and is the second-largest CO2 emitter in the Indian manufacturing sector (Garg et al., 2017). ... The average eco-efficiency value of the clinker calcination and cement grinding processes are 0.761 and 0. ...
Being an energy intensive industry, typically this segment of industry accounts for 50–60% of the total production costs [17].Thermal energy accounts for about 20–25% of the cement production cost [18].The typical electrical energy consumption of a modern cement plant is about 110–120 kWh per tonne of cement [19].The main thermal …
Grinding aid additives are established in various industrial dry fine grinding processes, primarily to achieve either a) an increase of the production capacity, b) a decrease of the specific energy consumption or c) finer particles or a better product …
Therefore, producing cement with less energy is becoming a key element of profitability: as the grinding process consumes about 60 per cent of the total plant electrical energy demand and about 20 per cent of cement production variable cost. So efficient grinding unit selection impacts profitability of cement manufacturing.
About 2% of the electricity produced in the whole world is used during the grinding process of raw materials [1]. While total electrical energy consumption for cement production is about 100 kWh/ton of cement, roughly two thirds are used for particle size reduction [2]. About 65% of the total electrical energy used in a cement plant is utilized ...
PDF | Grinding aids (GAs) are polar chemicals introduced in cement mills in either liquid or powder form to improve on mill grindability efficiency.... | Find, read and …
For drying and grinding it is state of the art to equip these types of grinding plant w i t h vapour recirculation and use either exhaust air from the burning process, clinker cooler exhaust air ...
The history of Cement Industry of Bangladesh is not as old as other countries have a deep-rooted legacy of construction materials. The attempt to produce cement in Bangladesh dates back to 1941 when the first Cement Factory called "Chattak Cement Factory Ltd" (formerly known as Assam Bengal Cement Company Limited) was …
The Effect of Various Grinding Aids on the Properties of Cement and Its Compatibility with Acrylate-Based Superplasticizer. January 2022. Materials 15 (2):614. DOI: 10.3390/ma15020614....
About CemNet e-Learning | Cement Industry Training. CemNet e-Learning courses provide a thorough learning experience for cement industry personnel, with a wide range of features designed to accelerate full understanding of the complete manufacturing process. Coursework, assessments, expert advice and an interactive approach, all …
In 2011, the direct CO2 emission factor and manufactured CO 2 emission factor of China's average cement manufacture is just 0.4778 t/t and 0.5450 t/t, respectively, and the direct CO 2 emission and manufacture CO 2 emission from China's cement industry is 0.9983 and 1.1364 Gt, respectively, from the life cycle view, carbon emission …
A typical raw mix consists of 75-85% limestone, 12-25% shale, the balance consisting of silica or quartzite and iron oxide. Exact proportioning is dependent upon their chemical properties before and after calcining to cement clinker. For good kiln practice the grind required is 88-92% – 200 mesh for standard cement, 99%-200 mesh for high early.
Introduction. Grinding aid or grinding additives refer to substances which when mixed into the mill contents cause an increase in rate of size reduction [1]. These terms are very …
حقوق النشر © 2024.Artom كل الحقوق محفوظة.خريطة الموقع