SCREEN CAPACITY CALCULATION
percentage of small feed material the greater the screen capacity. The faster the material passes through a screen the more open area there is left to screen the remaining material. A feed material with 40% of the feed being half the opening size or smaller equates to a factor of 1.0 . Figure 6 uses the percent of feed material half the
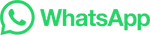