A REVIEW ON STUDY OF JAW CRUSHER
materials and tertiary and quaternary crushers reducing ore particles to finer gradations. This paper focuses on review of a work carried out by researchers in the field of …
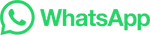
materials and tertiary and quaternary crushers reducing ore particles to finer gradations. This paper focuses on review of a work carried out by researchers in the field of …
A parameter study using a jaw crusher is designed to investigate the influence of feed gradation, feed rate, crusher setting and crusher speed on the crusher operation and the quality of the produced aggregates. ... As the throughput is reduced by about 50%, the reduced material density in the crusher results in less particle-to …
The Jaw Crusher is a primary sample preparation unit and is required for size reduction of various kinds of materials. Desired crushing takes place when fed particles experience pressure exerted by the jaw blade action. By this action the particles are crushed to smaller sizes. The product size will depend upon the crusher blade gap and feed ...
A primary jaw crusher is a machine designed to reduce large rocks into smaller rocks, gravel, or rock dust. It is used in many industries, including mining, construction, and demolition, to crush materials such as rocks, coal, and ores. A primary jaw crusher consists of two plates, one stationary and one movable, which form a V …
Rose and Hill (1967) considered crusher capacity by determining the amount of time and distance a particle takes between two jaw plates. Particles in the A-B zone discharges at the next reverse movement of the jaw. The maximum size of a particle dropping out of the crusher d max is determined by the open size setting (L max).
The jaw crusher angle and rotating mass type are considered to study all particle sizes and reduction ratios obtained for three different motor operation speeds: 1500, 2000, and 2500 rpm.
Jaw crushers are the most common solution in underground applications when the throughput is below 1000 tonnes per hour, depending somewhat on the scalping solutions. Above 1000 tph, …
What are jaw crushers? A jaw crusher is a crucial component in mining and ore processing plants, performing the primary crushing of rock and mineral ore to reduce and control …
In a jaw crusher, the material is crushed between two plates: a static plate and a moving plate. Compression is applied by the moving plate, and the material becomes crushed. ... The improved model of inter-particle breakage considering the transformation of particle shape for cone crusher. Minerals Engineering, Volume 112, 2017, pp. 11-18.
Process Parameters. Reactors. Separations – Chemical. Separations – Mechanical. Transport & Storage. Size Reduction. Raw materials undergo size reduction through different mechanisms: impact, compression, and …
The discharge conveyor and hopper under the crusher should be wider than the discharge width of the crusher. Sufficient tension must be placed on the toggle plate to ensure proper alignment. Feeding for efficiency. Jaw crushers are routinely choke fed to maximize production capacity and ensure that particles are uniformly broken.
A typical jaw crusher can accept boulders that are about 75-90% of the size of its gape (the distance between the jaws at the feed opening), which, for large crushers, can be up to 48 inches wide. Through the use of compressive force, the Jaw Crusher reduces these large boulders into pieces roughly 6 to 8 inches in size.
Q-5 A sample of materials is crushed in a Blake Jaw crusher such that the average size of the particles is reduced from 50 mm to 10 mm with the energy consumption of 13 kW/ [Kg/s]. Determine the consumption of energy to crush the same material of 75 mm average size to an average size of 25 mm using Kick's Law. Q-6 270 kW of power is required to ...
Retsch. Products. Milling. Jaw Crushers. The RETSCH Jaw Crusher range is used for the rapid, powerful crushing and pre-crushing of mediumhard, hard, brittle and tough materials. The variety of materials offered, their efficiency and safety make them ideal for sample preparation in laboratories and industrial plants. Benchtop Unit.
The difference between the cumulative percentages at the 3.5″ and 1.5″ points on the curve gives us the amount, of such product to be expected from the output of the primary crusher This is 85 minus 43, or 42% of the primary crusher product. If our problem had covered a crushing condition calling for 80 instead of 85% passing the …
5. Provide a well-graded feed. Another best practice for feeding Jaw Crushers is to blend the feed material ahead of the crusher to ensure a well-graded feed. This will produce steady, consistent tons per hour out of the Jaw Crusher. It will also promote inter-particle crushing to break any flat or elongated material.
PFC3D modeling of rock and jaw crusher. In order to examine the fracture behavior of the rocks and to determine the applied energy in a jaw crusher, a PFC3D model for the jaw crusher was developed. This model is based on single macro-particle simulation in a crusher, and multi-body interactions are ignored. The crushing process …
3.. Single particle breakage analysisThe fracture process of a rock in a jaw crusher is a series of single particle crushing events with increasing number in a power law manner (Refahi et al., 2007).The product emerging out of the jaw crusher is just a collection of progeny particles from the crushing process of numerous single particles.
The analysis will concentrate on jaw crushers as typical and widely used comminution process equipment. A jaw crusher (see Fig. 2) is a comminution device designed to impart an impact on a rock particle placed between a fixed and a moving plate (jaw).The faces of the plates are made of hardened steel.
The present work uses a Particle Replacement Model (PRM) embedded in the software EDEM® to model and simulate operation of a laboratory-scale jaw crusher. The PRM was calibrated using data …
Dodge Jaw Crusher: Similar to the Blake crusher, the Dodge crusher has a movable jaw that moves towards and away from the stationary jaw, and is preferred for crushing softer particles. Universal Jaw Crusher: This type has a "V"-aligned fixed jaw and a movable jaw on an eccentric shaft, creating an elliptical motion.
As an indirect jaw crushing parameter, the choke feeding intensity was also emphasized by Beloglazov and Ikonnikov [40]. As the rock comminution and energy efficiency can be defined as a function of area increment of particles in jaw crusher [41], the production of fines can be diminished by regulating the mf in the crushing chamber.
Particle size distribution curves of recycled aggregates from building demolition concrete crushed by jaw and impact crushers. The jaw crusher produced 60% of coarse aggregates in weight, whereas the impact crusher produced 49% coarse aggregates. The proportion of particles finer than 0.15 mm is around 7–8% weight for …
The main components of a typical jaw crusher are: Fixed Jaw; Moving Jaw; Jaw Liners; Main Shaft (Pitman Assembly) Drive Pulley & Flywheel; Toggle Plate(s) & Tension …
The obtained fractal dimensions of the particle size distributions for the particles crushed by the jaw, cone, and roll crushers were in the range of (2.16–2.38), (2.13–2.31), and (2.23–2.46 ...
The mechanism of movement of rocks down the crusher chamber determines the capacity of jaw crushers. The movement can be visualised as a succession of wedges (jaw angles) that reduce the size of particles progressively by compression until the smaller particles …
The obtained fractal dimensions of the particle size distributions for the particles crushed by the jaw, cone, and roll crushers were in the range of (2.16–2.38), (2.13–2.31), and (2.23–2.46 ...
A single toggle jaw crusher consists of an eccentric shaft that is placed on the top of the crusher. The rotation of the shaft along with the toggle plate generates the necessary compression force required to break down the substance into smaller particles. A single toggle jaw crusher has a better capacity than a double toggle jaw crusher.
The right jaw crusher for each application depends on the particle size, volume, and properties of the feed material, as well as the desired particle size and quantity of the final sample. Jaw plates are available in a variety of materials for most machines to adapt to the hardness properties of samples and to extend service life.
The right jaw crusher for each application depends on the particle size, volume, and properties of the feed material, as well as the desired particle size and quantity of the final sample. Jaw plates are available in a …
حقوق النشر © 2024.Artom كل الحقوق محفوظة.خريطة الموقع