Ball Mills working principle & advantages
A ball mill is a type of grinding machine that uses steel or ceramic balls to grind materials into a fine powder. It works on the principle of impact and attrition. Impact occurs when the balls are lifted by the rotating mill and then drop onto the material to be ground. The force of the impact breaks the material into smaller pieces.
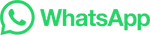