Used Grinding for sale in Greece. ICMA equipment
Used HSS Iron Disc Grinding Machine. used. schmidt tempo k4 Tempo K4, HSS machine for sharpening HSS discs, Conventional For blade diameter 20 mm to 350 mm Max. saw …
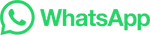
Used HSS Iron Disc Grinding Machine. used. schmidt tempo k4 Tempo K4, HSS machine for sharpening HSS discs, Conventional For blade diameter 20 mm to 350 mm Max. saw …
Key Benefits. Raise throughput while lowering energy consumption. Extend uptime with longer - lasting rolls. Advanced digital tools improve process and maintenance. No …
polycom® units are used for throughput rates in excess of 2,000 tph. The mill feed material can be dry or moist with a largest feed grain size of up to 60 mm. If necessary, the material can be predried. polycom® - High pressure grinding rolls. Explore the possibilities of advanced engineering through thyssenkrupp Polysius's innovative ...
The grinding elements of the Ultraplex UPZ fine impact mill are interchangeable, which allows the mills to be used as universally as possible. The Sugarplex SX pin mill was developed especially for the sugar industry. The Contraplex CW II wide chamber pin millis particularly suitable for oily products and can also be used for cryogenic grinding.
double-roller mill SPCII-C750S. for plastics fine cutting high-performance. Contact. Output: 150 g/min - 200 g/min. Features Very little dust The cutters do not re-cut sprues and runners in the same place so that the cutters can minimize dust, static electricity, and heat generation. Very few miscuts The cutters have the mechanism to cut the ...
Within comminution circuits, High Pressure Grinding Rolls (HPGR) are increasingly replacing conventional SAG, rod and ball mills for hard rock reduction – owing to their …
Important specifications when selecting grinding mills and pulverizers include, The size of the mill can range from pilot/lab to production, e.g., 3.5 to 1600 cu. ft. Feed size, material, and hardness of feed must be considered. Output size …
You've already forked shibang 0 Code Issues Pull Requests Packages Projects Releases Wiki Activity
The equipment costs are higher for a VRM than a ball mill, reflecting the greater complexity of the system, which includes items such as the rollers, table and the hydraulic system. Overall, when equipment, erection and civil costs are taken into account, the cost of a VRM project is around 20 – 25% greater than a ball mill system of the same ...
New & Used Grinding Mills for Sale. Savona Equipment is your source for grinding mills for grinding and crushing glass, wood, bone, and other materials. We buy, sell and …
As a rule of thumb, one should consider that the maximum particle size which would physically/effectively be nipped by the rolls would approximately be 1.75 times the size of the operating gap. Generally, depending on ore type and process conditions, the operating gap would be about 2.0–2.5% of the roll diameter.
High Pressure Grinding Rolls have lower maintenance overheads than ball and rod mills, primarily because the grinding media in conventional mills needs to be replaced on a more regular basis. This makes HPGRs more flexible when it comes to meeting your campaign timings. When tyres do wear down and need to be replaced, the Enduron® HPGR's ...
This paper presents the commercial implementation of a novel comminution circuit with high pressure grinding rolls (HPGR) followed by tower mill in a copper–lead–zinc ore dressing plant. With a throughput of 650 t/d, the comminution circuit comprises three stages of crushing by a jaw crusher, cone crusher, and HPGR as …
Vertical Roller Mills (VRM), High Pressure Grinding Rolls (HPGR), Vertical Shaft Impact Crushers (VSI) and more recently, Horizontal Roller Mill (Horomill) have saved the specific power by 45–70% when compared with a ball mill circuit [8], [10]. Now a days Ball mills and HPGR are installed together as a common unit.
The data relate to HPGRs operating with specific grinding forces typically in the range 2.5-3.5 N/mm2. The observed specific energies relate to power delivered by the roll drive shafts. Motor input power for full scale machines is expected to be 8-10% higher. Figure 6 – Observed vs Predicted HPGR Specific Energy.
High pressure grinding rolls HRC™3000 A step change in energy efficiency set the standard in high pressure grinding rolls (HPGR) when introducing the HRC™ HPGR. Designed from the ground up, focused on developing an HPGR that would be for hard rock applications and provide the lowest total cost of ownership.
Contribute to changjiangsx/sbm development by creating an account on GitHub.
An effect of a grinding method, that is ball mill and high pressure grinding rolls (HPGR), on the particle size, specific surface area and particle shape of an iron ore concentrate was studied ...
2.1 Experimental Design. The experimental planning with selected key factor like operating gap (X 1), applied load (X 2) and roll speed (X 3) was designed by CCD method to obtain the optimum conditions for grinding the BHQ iron ore in HPGR.A full second-order polynomial model was obtained by regression analysis for three factors by …
Used Makita grinding machines for sale in Greece. Find surface, cylindrical, belt and centerless grinders on Machinio.
Ring or disc mills use both inside and outside surfaces of a rotating circle for grinding. HPGR (high pressure grinding rollers), roll, or roller mills pulverize material as it moves between two large rollers or a roller and a …
Optimise your results with a high pressure grinding roll, an ultra energy efficient way to crush fine particles ... Our HPGR is a perfect complementary tool to work in conjunction …
Brief introduction to high pressure grinding mill. High pressure grinding mill is suitable for high fine milling processing of non-flammable and non-explosive materials with Mohs hardness less than 9.3 and humidity below 6% such as barite, limestone, ceramic, slag; its finished product size ranges within 80-425 mesh. If equip with special …
This paper summarises test results that were used to validate a model and scale-up procedure of the high pressure grinding roll (HPGR) which was developed at the JKMRC by Morrell et al. [Morrell ...
Coarse Grinding: AG mills are often used as the primary grinding stage in mineral processing circuits to reduce the size of ore particles before further processing. Reducing Maintenance: The absence of grinding media in AG mills reduces wear and tear on the mill's components, potentially leading to lower maintenance costs.
There are many factors that may make the mill body vibrate, including the grinding pressure, material layer thickness, air volume and temperature, accumulator pressure, wear condition of the roller and the grinding plate, etc. 3. The Grinding Pressure of the Mill. The grinding pressure is one of the key factors that have a great impact on the ...
This paper unifies high-pressure grinding rolls crusher (HPGR) models of the working gap, mass flow rate, power draw, and centre and edge product particle size distribution models to produce a framework that allows the simulation of the equipment for process optimization and control studies. Calculating the model parameters requires …
High-Pressure Grinding Rolls (HPGR) are now a proven technology in dry size reduction of ores in the minerals industry, being used in applications that range from tertiary and quaternary crushing ...
The energy consumption of the total grinding plant can be reduced by 20–30 % for cement clinker and 30–40 % for other raw materials. The overall grinding circuit efficiency and stability are improved. The maintenance cost of the ball mill is reduced as the lifetime of grinding media and partition grates is extended. 2.5.
Key Benefits. Raise throughput while lowering energy consumption. Extend uptime with longer - lasting rolls. Advanced digital tools improve process and maintenance. No grinding media required. Enhance the sustainability of grinding operations.
حقوق النشر © 2024.Artom كل الحقوق محفوظة.خريطة الموقع