Coal-Fired Boiler
Coal-fired boilers influence plants to release lignite rich in limestone that contains quicklime (CaO). It rapidly breaks down in water to form calcium hydroxide …
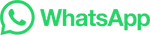
Coal-fired boilers influence plants to release lignite rich in limestone that contains quicklime (CaO). It rapidly breaks down in water to form calcium hydroxide …
1.1.3.2 Sulfur Oxides4 -. Gaseous SO from coal combustion are primarily. x sulfur dioxide (SO 2), with a much lower quantity of sulfur trioxide (SO 3) and gaseous sulfates. These compounds form as the organic and pyritic sulfur in the coal are oxidized during the combustion process. On average, about 95 percent of the sulfur present in ...
Up to 15% reduction in NOx with CO control. Up to 30% reduction in soot blowing. *Together with GE Asset Performance Management. Improve plant availability and …
boilers in the iron, steel and cement industries within the Good practice for industrial coal-fired boilers 5 range of 0.5–50 MWth and examines: pollution control requirements; control technologies; cost implications for industrial energy from coal. Currently there is no international best practice for efficient coal-fuelled industrial boilers.
Fuel Types: Combusting fuel is the ultimate source of the boiler's heat. Gas, oil, and coal are common sources of fuel. When coal is used, it is often crushed and heated to improve efficiency. ... boiler generates heat …
A method for predicting unburnt carbon in a coal-fired utility boiler has been developed using an image processing technique. The method consists of an image processing unit and a furnace model unit. The temperature distribution of combustion flames can be obtained through the former unit. The latter calculates dynamics of the carbon reduction …
Their steam boiler for milk processing are classified based on fuel type, including oil and gas-fired boilers, coal-fired boilers, and biomass-fired boilers. Oil and Gas-Fired Steam Boilers: WNS Series: The WNS series steam boilers have a thermal capacity ranging from 1 to 20 tons per hour and a working pressure of 0.7 to 2 MPa.
Direct combustion is the primary technology for processing coal fuel, and it is constantly being studied to reduce the resulting pollutants [12][13] [14] [15][16][17]. The formation of harmful ...
Boilers are designed for specific coal types and can encounter slagging, fouling, ash-handling, or other problems if a diferent coal type is used (Kitto and Stultz, 2005). …
Which Type of Fuels do Boilers Use? Combustion is the process of burning a fuel source. To create a reaction, there must be a fuel source, heat, and an oxidizing agent. ... Coal is a standard fuel source. …
boilers in the iron, steel and cement industries within the Good practice for industrial coal-fired boilers 5 range of 0.5–50 MWth and examines: pollution control requirements; …
A boiler is an enclosed vessel in which water is heated and circulated, either as hot water or steam, to produce a source for either heat or power. A central heating plant may have one or more boilers that use gas, oil, or coal as fuel. The steam generated isused to heat ... To acquaint you with some of the fundamentals underlying the process ...
4-1-1 Pulverized Coal Boilers In a PC boiler, the coal is first crushed in a crusher. Its size is further reduced to <200 J.tm in a pulverizer; it is then dried, heated, and blown into the burn ers of the boiler. Three systems for this process have been developed: storage or P. Basu et al., Boilers and Burners
Fluent software was used to calculate the coal/NH 3 co-combustion process in coal-fired boilers, and the standard k-ε two-equation gas-phase turbulence model was used to calculate the turbulence [30]. The radiation heat transfer was considered by the discrete ordinates (DO) radiation model with wide application range and high calculation …
from the boiler by over 25%, below the significant level of 200 mg/m3. Reburning was carried out using an integrated system consisting of the boiler and a fixed-bed 60 kW (GazEla) gasification reactor. The process gas was continuously introduced above the coal burner of the boiler. The process parameters of the boiler and the gasifier were also ...
Although biomass can be considered as analogous to coal for the combustion process, the size and shape of the biomass are expected to influence the combustion dynamics and emissions [10], ... combustion, heat-transfer and emissions from a 609 MW utility tangentially fired pulverized-coal boiler. Fuel, 81 (2002), pp. 997-1006.
However, the highly complex combustion mechanisms in coal-fired power plant boilers pose a significant challenge in direct modeling and optimization. To tackle this challenge, this study …
Depending on the source of its energy, boilers can be classified as coal-fired boiler, oil-fired boiler, gas-fired boiler, and biomass-fired boiler. Boilers for co-generation of steam in co-generation power plants are commonly used in many industrial processes. ... Three steps make up the combustion process in steam boilers: pre …
The boiler is a primary part of global heating system in power plants. The boiler system functions with the heat distribution system, heat-emitting system & control systems. Boiler is the main working component of thermal power plants. An industrial boiler is a closed vessel system that plays a vital role in various applications.
Simulation of the drying process of coal slime in a circulating fluidized bed boiler Co - combustion in CFB boiler is an effective location to utilize coal slime and recover its heating value [ 14 ]. However, coal slime has a large water content and high viscosity, the water evaporation process has an important effect on the drying and initial ...
How a Coal Plant Works. Coal-fired plants produce electricity by burning coal in a boiler to produce steam. The steam produced, under tremendous pressure, flows into a turbine, which spins a generator to create electricity. The steam is then cooled, …
The coal-fired boilers with a capacity of more than 35 t/h will be upgraded to meet the national and provincial energy efficiency standards and pollutant emission requirements [4]. ... [35] carried out a numerical simulation of the combustion process of the methanol boiler in 2016. She found that the ideal diameter-length ratio is 0.41. The ...
Basic oil processing produces only petroleum gas. 0.17.0: Coal liquefaction now produces 90 heavy oil, 20 light oil and 10 petroleum gas, consuming 25 heavy oil, 10 coal and 50 steam. 0.15.0: Added coal liquefaction oil processing recipe. 0.9.1: Added heavy oil cracking and light oil cracking. 0.9.0: Introduced Basic oil processing
Processing of Coal. ... Coal enters the boiler (furnace), where it is burned. This boils water, producing steam. The steam turns a turbine, powering a generator. The resultant electricity is passed through a transformer (which changes the voltage) and is then sent through transmission lines. The steam cools and condenses back to liquid water in ...
Some coal constituents are potentially toxic, trace metals/metal compounds bound with the coal's mineral and organic matter components. These trace species are released during the combustion process and may pose an environmental and human health risk depending on their abundances, physicochemical forms, toxicity, partitioning …
The principle of processing flame image and reconstructing 2-D/3-D temperature distributions in large-scale furnaces has been described in detail in [11], [12], [13]. The coal-fired boiler furnace is considered to be filled by gray emitting, absorbing and scattering medium of suspended particles, and surrounded by gray water-cooled surfaces.
Depending on the characteristics of the coal and the particular boiler application, the designer may chose pulverized coal (PC) firing, cyclone firing, stoker, or fluidized bed firing methods. Whatever method is applied, raw coal should be prepared before being fed into the furnace. The preparation process has a major impact on the combustion ...
The process of heating a liquid until it reaches its gaseous state is called evaporation. Heat is transferred from one body to another by means of (1) radiation, which is the transfer of heat ... Chain-Grate or Traveling-Grate Stoker Boiler Coal is fed onto one end of a moving steel chain grate. As grate moves along the length of the furnace ...
Evaporation: Fuel is burned in a boiler to heat water and produce steam. Expansion: The steam is expanded through a turbine, which turns a generator to produce electricity. Condensation: The steam is then cooled and condensed back into water in a condenser. Pumping: The condensed water is pumped back into the boiler to start the process over ...
Our pulverized coal (PC) boilers generate steam power for large-scale global power projects with up to 1,350 MW electrical output for coal units at pressures and temperatures that enable net plant efficiencies of up to 50%. Our two-pass and tower boilers can reach up to 330 bar/650 °C/670 °C in both single and double reheat configuration.
حقوق النشر © 2024.Artom كل الحقوق محفوظة.خريطة الموقع