Cone Crusher
Cone crushers have gained such wide acceptance that they may be regarded as standard in the intermediate-range size-reducing machines. A schematic diagram of a cone crusher is shown in Fig. 4.6 A.The drive is similar to that of a gyratory crusher. The inner cone or 'crushing head' is supported by the tapered concentric spindle, which is rotated by the …
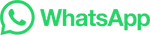