PTCL Infrastructure Ltd.
PTCL Iron Ore Beneficiation Plant. Recently commissioned with annual installed capacity of 1.5 Million MT located in the Mineral Belt with a huge potential for forward and backward Integration. Iron Ore Beneficiation …
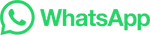
PTCL Iron Ore Beneficiation Plant. Recently commissioned with annual installed capacity of 1.5 Million MT located in the Mineral Belt with a huge potential for forward and backward Integration. Iron Ore Beneficiation …
Hence, it is necessary to beneficiate low-grade iron ore into commercial-grade to fulfil the demand for raw material for steel making. The Committee noted that beneficiation plants for iron ore with iron content between 45%-55% is rare in India because of poor economics. The cost of beneficiation is directly linked to power cost.
Since July 2020, all mines have been operationalised and in FY 2020-21, they collectively produced around 12.37 MnT of iron ore, which have been directed to our three integrated steel plants. Currently, we are exploring ways in which the production can be ramped up from the mines. Further, we are exploring setting up of beneficiation plant to ...
Golgohar pelletizing unit will be constructed in Sirjan by Golgohar iron ore company with production capacity of 5 million tonnes per year. Through a 470 meters long conveyor belt, Golgohar's concentrated outputs are transported to primary storage tanks, each with the capacity of 2000 tonnes. One of the reservoirs is dedicated to hematite ore.
The iron ore production has significantly expanded in recent years, owing to increasing steel demands in developing countries. …
Iron ore market issues. The over-arching issue is the flight to quality in China: improvement of the environment and lower CO2 emissions. production curtailments - winter heating season. sinter and pelletising plants shut down. improvement in blast furnace productivity. Declining grades and increased acid gangue in iron ore.
Slurry tank for storage of concentrated iron ore slurry from beneficiation plant. The particle size of iron ore in the ore slurry is less than 45 micro meter for around 80 % of the particles. Additive materials (such as dolomite, limestone, lime or olivine etc. depending on the quality of the pellet to be produced) is added to the slurry.
Brahmani River Pellets Limited is one of the largest merchant pellet manufacturers in India with a Pellet manufacturing capacity of 4 MTPA supported by beneficiation capacity of 4.7 MTPA. The manufacturing facilities of the Company are strategically located in the state of Odisha. Its Beneficiation Plant is located at iron ore hub of Odisha ...
KIOCL is having facilities to operate 3.5 MTPA Iron-oxide Pellet Plant, Blast Furnace Unit to manufacture 2.16 lakh tonnes per annum Pig iron at Mangaluru, Karnataka.KIOCL is an EoU and a profit making, continuous dividend paying Company with a positive net worth and Mini Ratna Category I PSU is also an ISO9001:2015, ISO14001:2015 and ISO45001 ...
A passion for pelletizing and consideration of the entire process chain from start to finish are fundamental to innovative pelletizing-plant solutions. Raw-material testing, mathematical simulation, 3D planning, and process automation are key elements Primetals Technologies brings with its passion for innovation to the iron and steel industry.
West Bengal. Rashmi Udyog Private Ltd (Rashmi Group) Paschim Midnapur. 1.2. 26. West Bengal. Orissa Alloy Steel Pvt. Ltd. (Rashmi Group) Kharagpur. 3.
Next. Beneficiation of Iron Ore and the treatment of magnetic iron taconites, stage grinding and wet magnetic separation is standard practice. This also applies to iron ores of the non-magnetic …
This Pelletizing Process develops best pellets for DR plants (HK Naik et al) A pellet plant contains a series of balling drums where the iron ore concentrate is formed into soft pellets, in almost the same manner that one rolls a snowball, to make a pellet about the size of a marble (between 1/4" and 1/2").
Therefore, the generated waste iron ore beneficiation plant tailings (IOBPT) containing 56.96% Fe(T), 4.07% Al 2 O 3, 7.23% SiO 2 and 4.38% of LOI (contributed mainly from clay and goethite) can be considered a potential secondary mineral resource consumed in the downstream iron making processes. In the current investigation, a …
Our iron ore pelletizing systems combine the best features of both technologies to provide the most modern plant and to produce pellets at the lowest cost and highest quality. Pellet plants sized from 1.2MTPA to 9MTPA. Engineering and design of complete plants from ore receiving to pellet discharge. Supply of the main pelletizing and indurating ...
technology for iron ore pellet processing, which is based on over 60 years of experience and world-class R&D. This process produces pellets with excellent physical and …
It is India's first low-grade iron ore beneficiation complex with an integrated slime dam. The plant is located at Kalinga Nagar, Odisha, and iron ore is fed through a 230 km slurry pipeline commencing at Barbil, Odisha. Subsequent to the takeover, BRPL's production increased by 33%, and conversion costs decreased by 15%.
Our iron ore pelletizing systems combine the best features of both technologies to provide the most modern plant and to produce pellets at the lowest cost and highest quality. …
The comprehensive project comprises various units, such as iron ore beneficiation, pellet plant, coke oven, power plants, and steel production units. With an estimated cost of Rs. 89,170 million, the project is currently undergoing clearance procedures from the Ministry of Environment, Forest and Climate Change of India
1.5 Project Cost 6 2 Introduction of the Project / Background Information 7-10 ... Iron ore Beneficiation plant:1.6 MTPA Pellet Plant: 1.2 MTPA (2X0.6 MTPA) Sponge Iron: 2,31,000 TPA WHRB: 16 MW (2X8MW) Ingots/Billets: 1,98,000 TPA, ... significant shift in respective share of lumps and agglomerated iron ore (pellets) and
Re-beneficiation of iron ore tailings from the conventional beneficiation plants ... shaft kiln pellet plants are approximately 50% of the investments on chain grate furnace cum rotary kiln type pellet plants. The cost of making pellets will be only Rs. 750 per ton in the vertical shaft kiln, as against to Rs. 1,500 per ton in the chain grate ...
Assuming the highest cost calculated in the "Cost analysis of iron losses due to an ore beneficiation and a scrap upgrade" …
three decades, consumption of iron ore has increased rapidly. In the metallurgy of iron ore, blast furnace utilize different form of products of iron ore like lumps (which used directly in the furnace) & pellet / sinter which are normally agglomerates of iron ore fines. Both the form of iron ore contain : 2: O: 3 (alumina). India is one of < 2% ...
As a result of resource depletion, rejected fines of low grade ore are the first thing that people notice. Due to the presence of high alumina and hydrous iron phase, the iron ore from Bonai ...
The iron ore pelletizing process consists of three main steps: 1. Pelletizing feed preparation and mixing: the raw material (iron ore concentrate, additives. — anthracite, dolomite — and ...
In the present study a detailed characterization followed by beneficiation of low grade iron ore was studied. ... it is possible to obtain pellet grade concentrate with 65.41% Fe, 2.54% SiO2, 2.79 ...
Iron ore is the basic raw material for iron and steel making. India is among the leading producers of iron ore in the world and produces about 150 million tons per annum (U. S. []).The total reserves of iron ore in India is around 28.5 billion tons, of this hematite ore is considered to be the most important iron ore because of its high grade …
The haematite ore in South Africa is processed in a dry process to a HQ lump ore with 64 % iron content and a sintered fine ore with 63.5 % iron content. For fine ore beneficiation, wet processes are used. Capacity at the Minas Rio is to be increased from 26.5 Mta capacity to 28 Mta in the forthcoming years.
will be used for captive consumption in the company's sponge iron plants as well as will be sold in the open market. 1.2 Details of Products Proposed 2.4 MTPA Pellet Plant - Input and Output % Per hour Per Day Per year Raw Material Iron ore fines (t) 95.91 340.00 8,160 26,92,800 Bentonite (t) 0.71 2.50 60 19,800
Abstract. Flotation is the most effective solution, both technological ly and economically, w hen upgrading. iron concentrates. Research regarding iron ore flotation began in 1931, demonstrating ...
حقوق النشر © 2024.Artom كل الحقوق محفوظة.خريطة الموقع