Pre-Processing to Increase the Capacity of SAG Mill …
Both changes were thus beneficial to the SAG mill performance compared with the SAG-2 test performance (7.8 kWh/t), where both ball charge and mill speed were relatively low. Such a result is …
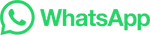
Both changes were thus beneficial to the SAG mill performance compared with the SAG-2 test performance (7.8 kWh/t), where both ball charge and mill speed were relatively low. Such a result is …
The total amount of steel in the mill building, approach, tail-track and power plant structures is approximately 7,000 tons. The total cost of mill and equipment, according to the published report of the United States Steel Corporation, approximates $1,500,000.
Based on the results of the overview, a future processing plant is predicted to use ∅12.8–13 m SAG mills, HPGRs with the roll diameter of 3 m, vertical VTM-7000 mills in ore grinding cycles ...
Application in CIL Plant. SAG mill can be applied as the first stage grinding equipment. It can effectively avoid the occurrence of sliming phenomenon, and avoid further grinding of fine particles. It can play a good role in …
with an AG mill or with an SAG mill. 2.2.2 Separation The ground material is separated into useful ore and impurities in a separation process. Two types of separators: i.e., a separator based on the difference in Fig. 1 Example of process flow in beneficiation plant 9 KOBLCO TCHNOLOGY RI NO. 33 FB. 215
Multiple stages may include a rod mill followed by a ball mill (two stage circuit), or a semi-autogenous grinding (SAG) mill followed by a ball mill (two stage circuit). Smaller plants tend to add extra crushing stages in order to operate a single grinding stage only. If a ball mill uses little or no water during grinding, it is a 'dry ...
Mill Discharge Slurry Pump – Buy Mill Discharge Slurry …. Mill Discharge Slurry Pump, …. Sump Slurry Pump. FOB Price: US $356 – 2996 / Set. Port: TIANJIN Min.Order: 1 Set/Sets Starch Slurry Pump. FOB Price:
SAG Mill Success—Start with the Basics – WOMP – World of …. SAG Mill Success —Start with the … for overall design of the motor, mill and foundation to any one specific entity, they do offer specific guidelines for … » More detailed Choosing a SAG Mill to Achieve Design Performance. Key Words: SAG mill, design, optimum conditions, …
ZJH Minerals is professional manufacturer for the AG/SAG mills of diameter less than 10m. AG/SAG mills are widly used for grinding of the non-ferrous ore and the black ore and the nonmetal ores,especially suitable for grinding the ores in which the useful minerals are coarse-grained and uniformly distributed.Ball mill used in the Site.
immediately available for reuse in the beneficiation plant because it has been used in the production of backfill slurry from tailings to provide underground mine support; because it has been entrapped in the ... water usage. The crushed ore is transferred to a semiautogenous (SAG) mill or ball mill where the ore is further reduced in size ...
Many designers and mill operators believe that the benefits of simplicity and the ability to handle throughputs in excess of 3 500 tons per hour of solids make trommels the preferred equipment for this application. "A …
Many studies were conducted in organizations such as KCGM in Western Australia, Porgera in Papua New Guinea, Highland Valley in British Columbia, and Cadia Hill in New South Wales. Improvements in ...
Step 1: Milling. When ore enters the plant from underground it first needs to be milled to reduce its size so that the gold is liberated from the host rock. South Deep's milling circuit consists of a single-stage semi-autogenous grinding mill (SAG) and a pebble crusher for primary milling, followed by secondary milling using two overflow ball ...
The sag mill grinding ball produced by ZJH minerals is high-tech wear resistant products for different mines. Our grinding balls are researched relies on the scientific research team composed of experts and scholars in the field of wear resistance. It has the characteristics of high toughness, high strength, high wear resistance, high corrosion ...
The Iranian Gohar-Zamin iron ore beneficiation plant consists of equipment such as gyratory and cone crushers, high pressure grinding rolls (HPGR), ball mill, dry and wet double-deck vibrating ...
Mining/Mineral & Ore Processing — Beneficiation ARC IBX1 Coating Case Study 080 SAG Mill Discharge Chute Challenge Issue Failure of a rubber and tile lined chute caused leaks and unscheduled outages with lost production costs of >$115K/per day. Goal Plant sought increased MTBF of chutes. Root Cause Seams in rubber lining exposed to highly
WET SAG MILL. The wet self-grinding machine/semi-self-grinding machine is a kind of equipment which uses the ore itself to crush and grind. The barrel has larger diameter, shorter length and larger feeding size, which can replace medium crushing, fine crushing and coarse crushing. Production Process. Generally, the amount of steel balls added ...
Tang-e- Zahg Iron Beneficiation Plant. Feb 2023 - Present 1 year 3 months. Hormozgan Province, Iran. Improving the efficiency of the ball mill, enhancing the feed rate within the grinding circuit, and guaranteeing high-quality production by implementing ongoing monitoring of the spiral circuit.
The rapidly developing mining industry poses the urgent problem of increasing the energy efficiency of the operation of basic equipment, such as semi-autogenous grinding (SAG) mills. For this purpose, a large number of studies have been carried out on the establishment of optimal operating parameters of the mill, the …
The larger units can also be matched with the SAG mill in SAB/SABC configuration. Stirred mills (Regrinding). Finer regrinding or ultra-fine grinding is a frequent requirement in pilot plants and ALS has a range of …
Additional applications of machine learning to SAG modeling put the focus on the control of SAG grinding mill circuits, predicting power consumption [90, 91], one of the main concerns of plant ...
• SAG Mill Comminution (SMC) • SAG Pilot Plant Beneficiation Beneficiation is the process where ore is reduced in size and gangue separated from the ore. Separation …
The tie-in of pilot plant SAG mill results to commercial comminution, using minus 1-inch crushed diamond drill core for feed, is the breakthrough discovery that has allowed pilot …
Typical types of mill used in ore beneficiation are autogenous (AG) and semi-autogenous (SAG) mills together with ball mills to, for example, obtain particle sizes smaller than 100 µm. One process variation that has become increasingly established in recent years is the combination of AG or SAG mill with a ball mill and a downstream agitated ...
reasons for the attraction for SAG milling are circuit simplicity and typically lower capital and operating costs to meet the needs for operations with higher throughput. SAG mills work well for handling clay rich sticky ores, which is a challenge for multistage crushing circuits requiring washing plants. 4 Beneficiation of Gold and Silver Ores
The iron ore beneficiation plants normally include a series ... The feed rate of Ball mill in the second plant is lower and it has a finer product. ... semiautogenous grinding (SAG) and two stage ...
Shenyang Northern Heavy Industry Co., Ltd.(SNM) was founded in 2010 as an engineering service and heavy industry equipments supplier. SNM is recognized as an expert in providing process design, plant …
Various configurations of weir bars and scrolls are used to increase retention time and regulate the flow of solids through the trommel screen. Multotec has supplied a number of trommel screens for 38' to 40' SAG mills that required 500 to 600 mm-high weir bars to create sufficient retention time. Super Scroll.
Online condition monitoring system for SAG Mill & Ball Mill gear boxes to improve reliability. Repairing of concrete reinforcement of Pb, Zn & Tailing thickeners to ensure structural and equipment safety ... SKM has also recently commissioned an Integrated Control Room for mine and beneficiation plant operations from a single room. …
The application of autogenous/semi-autogenous (AG/SAG) mills is widespread in industrial mineral processing plants as first stage-grinding units for ore size reduction, mineral liberation purposes, and economic benefits [1,2,3].These mills are used for grinding large quantities of ores of varying characteristics, which presents control …
حقوق النشر © 2024.Artom كل الحقوق محفوظة.خريطة الموقع