Working Principle of Crushers
The gyratory crusher is used as a primary and secondary stage crusher. The cone crusher is used as a secondary, tertiary, and quaternary crusher. The action of a typical gyratory-type crusher is …
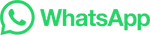
The gyratory crusher is used as a primary and secondary stage crusher. The cone crusher is used as a secondary, tertiary, and quaternary crusher. The action of a typical gyratory-type crusher is …
Primary crushing in the mining industry refers to the initial stage of reducing large rocks or ore into smaller pieces. This is typically done using mechanical equipment such as jaw crushers or gyratory crushers. ... The primary crusher's capacity is a critical factor in ensuring that the anticipated volume of raw material extracted from the ...
Primary Crushing. The purpose of the primary crusher is to reduce the ROM ore to a size amenable for feeding the secondary crusher or the SAG mill grinding circuit. The ratio of reduction through a primary crusher can be up to about 8:1. Feed: ROM up to 1.5 m; Product: -300mm (for transport) to -200mm (for SAG mill) Feed Rate: 160 to 13,000 tph
The crushing process involves the use of crushers to break down rocks and stones into smaller sizes. The primary crusher is used to reduce the size of the initial rocks, while the secondary crusher further breaks down the smaller pieces into finer materials. Purpose and Benefits of Using Primary and Secondary Crushers.
Jaw crushers are the most common solution in underground applications when the throughput is below 1000 tonnes per hour, depending somewhat on the scalping solutions. Above 1000 tph, primary gyratory crushers are an option. After the throughput reaches 2000 tph, jaw crushers are very rare, with the exception of a parallel plant layout.
Superior™ MKIII primary gyratory crushers all can include SmartStation, which combines innovative monitoring tools. Tools such as **VisioRock® and VisioTruck® along with expanded sensors on the equipment and …
Primary Crushing Merupakan tahap penghancuran yang pertama, dimana umpan berupa bongkahanbesar yang berukuran +/- 84x60 inchi dan produknya berukuran 4 inchi. Beberapa alat yang digunakan dalam proses primary crushing ini adalah : Jaw Crusher Alat ini mempunyai 2 jaw, yang satu dapat digerakkan (swing jaw) dan yang lainnya tidak …
Jaw Crushers are a popular choice for the primary crushing of a variety of materials, including hard, abrasive and non-friable materials that may be wet but are not sticky.. Crushing of the material takes place between a stationary and moving or swing jaw plate. The swing jaw plate is mounted on a pitman, which is given a reciprocating motion.
Outotec's line of Superior™ Primary Gyratory crushers are designed to meet the demand for high efficiency and high capacity mining installations. Superior™ MKIII is the first high speed Gyratory. The new features allow significant CAPEX reduction of a primary crushing stage from the retaining wall to the primary stock pile.
Primary crushing is the first important step in turning big materials into smaller pieces. It makes everything that comes after work better and faster. It's really important to know about the different main crushers, what they do …
A gyratory crusher is a type of large primary crushing equipment used in the mining, aggregates, and construction industries. Its processing capacity is as high as 14,082 t/h, and the feed particle size can reach 1,350 mm. It handles medium to high hardness and aggressive materials. Therefore, it is ideal for dry to slightly wet materials, but ...
Blake jaw crushers, also as double toggle jaw crushers, are characterized by the position of the pivot of the swing jaw, which is located at the top of the machine. This design allows for a larger feed size and a higher capacity, making it suitable for primary crushing. The motion of the swing jaw in a Blake crusher is predominantly vertical ...
Model A Primary Crusher. Parallel shaft gearboxes drive coarse or fine grind output. Coarse-ground materials 1-4". Fine-ground materials 1/2-2". Fine grind increases output. Minimizes wear and additional processing by secondary/tertiary grinders. Available with coarse and fine grind options. Ductile iron discs mounted on an 8-inch square ...
The primary crusher is the equipment that reduces the size of the materials to the size that can be processed by the secondary crusher. The primary crusher receives the materials directly from the mine or …
Liberty® Jaw Crusher. Primary. Maximum Feed Size 47″ (1,194mm) Maximum Reduction Ratio 6:1. Maximum Production Rate 1,595 STPH (1,446 MTPH) — Materials: Ore/Hard Rock, Quarried Stone, Recycled Asphalt, Recycled Concrete, River Gravel
Primary Crusher: At the core of every primary crushing plant is the primary crusher, which is responsible for breaking down the raw material into smaller pieces. Common types of primary crushers ...
The Cedarapids® CRJ3042 plant combines the popular JW42 jaw crusher with a high stroke, 42" x 20' (1067 x 6096 mm) vibrating grizzly feeder resulting in a high production portable crushing machine. This plant includes a hopper design that can handle severe primary crushing applications. The highly mobile CRJ3042 is easy to operate and ...
Increase productivity with a revolutionary roll crusher The ERC 22-20 is a revolution in primary crushing that delivers increased capacity, reduced energy consumption and lower operating costs. With the two-machines-in-one concept, combining a crusher and a screen, the ERC 22-20 has a compact design that simplifies transportation, installation
Primary crushing brings run-of-mine ore down to a maximum size of the order 4″ to 6″ in average diameter; secondary crushing receives feed at −6″ and reduces it to below "Dry" crushing includes work on ore as mined, which may be somewhat moist when delivered. It is succeeded by comminution in water, arbitrarily called "grinding".
Learn about the key differences between primary and secondary crushers and their respective functions in the mining and construction industry. Discover real-world applications and when to use …
Underground primary crushing station (Fig. 3) is generally fixed. It is usually located next to the skip shaft and is characterized by long service life, long infrastructure time, etc. The main equipment of the primary crushing station includes a crusher, feeder, dedusting apparatus, crane, etc. The primary crusher is mainly divided into ...
There are several types of primary crushers, including: Gyratory Crushers. Jaw Crushers. Hammermills. Horizontal Shaft Impact Crushers. Sizers. Roll Crushers. Cone Crushers. Feeder-Breakers. Gyratory Crushers are an excellent choice for a primary crusher, as they can handle very hard and … See more
Compression mining crushers solutions for breaking down hard minerals and ores. Enjoy optimum performance and reduced cost with compression crusher equipment and products. For over a century, FL has been renowned as the preferred crushing technology provider for mining and related industries.
L&T Reversible Impactors are proven equipment for secondary and tertiary crushing applications. The Reversible Impactors are improved versions of hammer crushers. The hammer size & impact blocks designs are made …
1. Identify The Purpose Of The Crusher. The first step in selecting a primary crusher takes place at a high level. It's necessary to identify the purpose the crusher will be used for. This purpose is a given …
The crushing plant can be provided with almost any type of primary rock crusher. The rock/ore determines the type of crusher. The plant capacity determines the size of the crusher. As the term 'primary' implies, these crushers are used in the first stage on any size reduction cycle. The primary crusher is the link between chemical ...
Each type of crusher for each specific crushing stage is explained in greater detail below. Primary crushing equipment. As the name suggests, this kind of crushing is the first in the process. Run of Mine (ROM) materials are brought directly from blasting projects and crushed a primary crusher for the first round of crushing.
9 Crusher Automation 9 Visiorock 10 Wear Parts - Crushers 11 Customer Service 12 Standards and Technical Infromation 13 Minerology and Testing ... primary mobile crushing plant to fur-ther processing stages. They are able to follow the primary unit as it moves along the quarry face, replacing costly dump truck haulage. ...
A primary jaw crusher is a machine designed to reduce large rocks into smaller rocks, gravel, or rock dust. It is used in many industries, including mining, construction, and demolition, to crush materials such as rocks, coal, and ores. A primary jaw crusher consists of two plates, one stationary and one movable, which form a V …
Selecting the right crusher for each stage of the crushing process depends on an understanding of the material to be crushed and the site's production goals. Jaws and gyratories will most often be found in the primary crushing stage, while cones, impactors and roll crushers are most often used in the secondary, tertiary and quaternary ...
حقوق النشر © 2024.Artom كل الحقوق محفوظة.خريطة الموقع