Mastering Process Control Instrumentation in Cement Plants…
Without process control instrumentation, it would be nearly impossible to maintain consistent quality and efficient operations in a cement plant. ... Implementing a control and instrumentation system for cement plants involves several steps. The first step is to perform a detailed analysis of the process to identify the critical parameters that ...
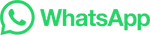