(PDF) Operational parameters affecting the vertical roller mill
Pilot plant test results with various ores showed that low energy consumption feature of vertical roller mills is applicable to the ore industry. Grinding test results for zinc ore showed that it is possible to decrease the total grinding energy consumption from 20.11 to 11.40 kW h/t by using vertical roller mill instead of AG/SAG-ball mill ...
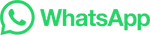