Difference Between Up Milling and Down …
Down Milling. In up milling, cutter rotates against the direction of table feed. In down milling, cutter rotates along the direction of table feed. Chip load on teeth (or uncut chip thickness) increases …
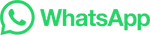
Down Milling. In up milling, cutter rotates against the direction of table feed. In down milling, cutter rotates along the direction of table feed. Chip load on teeth (or uncut chip thickness) increases …
You will end up with a crooked slot. 2 flutes stay on center because both flutes are in contact at the same time. A 4 flute endmill has 3 flutes in contact, therefore 2 flutes are pulling 'left', so it will wander. 4 flute endmills are best used for side milling. 2 …
Milling with cutting fluid. There are some exceptions to when cutting fluid should be used: Finishing of stainless steel and aluminum – to prevent smearing metal particles into the surface texture. Milling of heat resistant alloys at low cutting speeds – to lubricate and to cool down the component. Milling in cast iron – to dampen and ...
The 1/4" down bit, the workhorse of CNC router bits! This will be your first go-to bit with your CNC router. You will want to make sure it's a good one. Cutting diameter: 1/4" (0.25 inches) Shank: 1/4" / Length: 2.51" / Flutes: 2 / Flute length: 1.0". carbide, lasts 50x longer than traditional CNC router bits.
The Up-Cut Bit. One of the biggest advantages of the up-cut bit, is the ability to rapidly evacuate chips out of the area that the bit is cutting. This is very important, especially when cutting hard materials, like aluminum, deeper than 1/8″ where you run the risk of recutting chips, which can ruin the finish, cause chatter, or break the bit.
Some will say "Climb milling versus conventional milling" while others say "Down milling versus up milling." They're one and the same: Climb milling = down milling; ... This is a measure of how much material each tooth of the endmill is trying to cut. Typical values for finish work would be 0.001 to 0.002 inch per tooth.
The machining industry generally considers micromachining and miniature end mills to be any end mill with a diameter under 1/8 of an inch. This is also often the point where tolerances must be held to a tighter window. Because the diameter of a tool is directly related to the strength of a tool, miniature end mills are considerably weaker …
Reduced neck end mills provide maximum strength in long reach and deep pocketing applications. Like all Helical Solutions tooling, Reduced Neck End Mills are fully stocked …
Circular ramping is always preferred to linear ramping (full slotting), because helical interpolation is a much smoother process, as the radial cut is reduced. It allows for pure down-milling and provides better chip evacuation. Counterclockwise rotation ensures down-milling. Two-axis ramping – linear How to apply rampingA demanding cutting ...
For longer tool life and a better finish in general purpose milling applications, these solid carbide end mills are harder, stronger, and more wear resistant than high-speed steel and cobalt steel end mills. Their extreme hardness means they are brittle, so a highly rigid setup, such as a CNC machine, is necessary to prevent the end mill from …
Down milling. In down milling (climb milling), the cutting tool is fed in the direction of rotation. Down milling is always the preferred method whenever the machine tool, fixture and workpiece will allow for it. In peripheral down milling, the chip thickness decreases from the start of cut, … See more
Before we start milling away our stock we first need to get down to the required depth. ... When milling plunging into steels and other tougher materials, or when chip welding becomes an issue it is possible to straight-plunge into a smaller pre-drilled hole. ... Ramp chipload adjustment for 4 flute Center cutting end mills: 0-2.5deg= …
End mills are the workhorses of CNC Milling and use cutting flutes to remove material. DATRON Single flute end mills are ideal for material removal and roughing, as they are able to remove more chips per revolution with their large cutting channel and can be run at higher speeds thanks to their patented counter-balanced tip.
With CNC milling, the radius of your end mill is the radius of any internal corner, so you will almost never have a perfectly square corner on the inside of a milled object. Smaller and smaller end mills can be …
Plunge Milling is a type of CAM Toolpath, though it can be programmed manually as we will see. The idea, is to rough out a pocket, profile, or 3D surface by plunging either a twist drill, an endmill, or a special-purpose milling cutter straight down into the material. Here's a typical example:
In down milling (climb milling), the cutting tool is fed with the direction of rotation. Down milling is always the preferred method wherever the machine tool, fixture and workpiece will allow. In peripheral down milling, the chip thickness will decrease from the start of cut, gradually reaching zero at the end of cut. This prevents the edge ...
End milling is selected for shorter, shallower slots, especially closed grooves and pockets, and for milling keyways. End mills are the only tools that can mill closed slots that are: Straight, curved, or angled; Wider than tool diameter, designated pockets; Heavier slotting operations are often performed using long-edge milling cutters. Choice ...
This 1/8″ flat down cut end mill is a great, general purpose tool for milling soft and medium hardness materials like wood, plastic, and . This item comes in three and ten bit packages. An 1/8″ Precision Collet or a 1/4″ to …
CNC machining is a subtractive process that uses rotational cutting tools called "end mills" to remove material. An end mill, while similar in appearance to a drill bit, is far more versatile. However, in practice the terms "bit" and "end mill" are often used interchangeably. Drill plunging axially on left, endmill cutting laterally ...
Well-Known Member. Jul 1, 2023. #1. Looking for some detail on HOW to mill the liners to create integral bolsters. Pictures sketches print copies. Any and all wood b very very helpful snd appreciated. Yes i know there ate some for sale between 900-1500$. But retired and only working on knives as a hobby just this seems extreme for me.
Cut Width, also called Stepover, is the total thickness of the cut when viewing the cutting tool from above. It can be no more than of the cutter's diameter. Stepover is also referred to as Radial Depth of Cut. For the sake of completeness, Cutting Speed is defined as your spindle speed (in rpm) in the cut.
Carbide-Tipped Double-Chamfer End Mills. These carbide-tipped end mills provide a sharper, harder cutting edge and better wear resistance than high-speed steel without the brittleness of solid carbide. Their teeth are angled on both sides so you can make top and bottom chamfer cuts without having to flip the workpiece.
Download Now. Need Expert Advice? Get in touch with a trained WIDIA expert to discuss your metal cutting needs. Contact A Machining Expert! WIDIA solid end mills provide …
Down Cut Single Flute End Mill. View Available Options. Add to Favorites. In applications when the top surface is highly susceptible to chipping or fracturing, the down cut spiral …
Uncoated end mills are good for general purpose milling and short production runs. Use titanium aluminum nitride (TiAIN) coated end mills for demanding, high-speed jobs in hard material and for longer production runs. TiAIN coated end mills are more wear resistant and dissipate heat better than uncoated end mills, especially at high speeds.
HQMaster Downcut Bit 1/8" Shank Down Cut Spiral CNC Router Bits End Mill Tungsten Carbide Milling Cutter Set 5 Pack (3.175mm) 4.6 out of 5 stars 262. 100+ bought in past month ... SpeTool Downcut Spiral Router Bits 1/4 inch Shank,1/4 inch Cutting Diameter Solid Carbide CNC Router Bit Woodworking End Mills for Wood Carving Slotting. 4.6 …
Down cut CNC end mills are great for dado, pocket and inlay work as well as the final pass on most projects. These down cut end mill bits are especially useful when routing material such as melamine and plywood. …
Recently updated on March 14th, 2024 at 09:27 am. Find the perfect CNC end mill for your project with the ultimate guide at CNCCookbook. Discover tips, tricks, and the best …
End Mills. Improve the efficiency of your milling operations and add versatility with top-quality end mills, available now! MSC Industrial Supply's mission is to help you achieve outstanding results when performing numerous machining operations, such as chamfering, roughing, and finishing. We always maintain a vast inventory of different types ...
Round inserts and concepts with radius are milling cutters used for roughing and semi-roughing while ball nose end mills are milling cutters used for finishing and super-finishing. ... Down milling with a cutter tilted approx. 10° in two directions ensures a good surface finish and reliable performance. A ball nose cutter or a radius-shaped ...
حقوق النشر © 2024.Artom كل الحقوق محفوظة.خريطة الموقع