Gyratory Crusher (Gyratory Crushers Explained)
A crusher is a machine designed to reduce the size of Run of Mine (ROM) large rocks to smaller rocks, gravel, sand, or rock dust; this is essential for efficient transport of the ore via conveyors etc. Crushing is the first of …
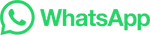