The six main steps of iron ore processing
1. Screening. We recommend that you begin by screening the iron ore to separate fine particles below the crusher's CSS before the crushing stage. A static screen is used to …
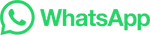
1. Screening. We recommend that you begin by screening the iron ore to separate fine particles below the crusher's CSS before the crushing stage. A static screen is used to …
Installation. Unzip file and place PAK file in the Pal/Content/Paks folder. This mod adds the following recipes to the crusher: Ore - 10 stone, 10 work amount. Coal - 10 stone, 20 work amount. Sulfur - 20 stone, 20 work amount. Quartz - 40 stone, 30 work amount. Pal Fluids - 3 Paldium for 2 fluids. There are 2 variations of this mod.
This paper summarizes more than a decade of systematic studies of the flow field in an iron ore pelletizing rotary kiln using computational fluid dynamics (CFD) on simplified models of a real kiln. …
Corporation's press release on January 5, 2024, at 09:00 a.m. EET. has received an order from Winning Consortium Simandou (WCS) for the supply of key crushing equipment for their concentrator plant at Simandou Iron Ore Blocks 1 and 2 in the Republic of Guinea. The value of the order exceeds EUR 10 million, and it is …
In light of these challenges, in-pit crushing and conveying (IPCC) is a technology that has grown in popularity since it was first implemented in the 1950s. The purpose of an IPCC system is to ...
Marketing is the international language of business. Our recent report forecasts that the Iron Ore Crusher Market size is projected to reach approximately USD XX.X billion by 2031, up from USD XX ...
State-of-the-art processes and technology for sustainable and safe operations. View solutions Spares, wears and services Parts for metals refining ... An optimal crushing process reduces the ore to a desired size more efficiently, economically and safely. The high-capacity, reliable and energy efficient crushing solutions deliver superior ...
Ore crushing methods generally include the following: mechanical external force crushing, electrothermal irradiation crushing, electrohydraulic effect crushing, …
Edison planned to process 1200 tons of iron ore every twenty hours. The plant had three magnetic separators that could produce a total of 530 tons of refined ore. There was other equipment to re-refine what was left over to extract even more ore. But technical problems persisted. In 1892, Edison shut down the mill in the hopes that …
For example, iron ore is often shipped directly from the mine to the customer. Since the tonnages involved are immense, extensive work has already been carried out to model the way that iron ore ...
The Joyce Lake DSO iron ore project will involve a conventional drill, blast, load and haul open-pit mining operation. The project envisages the development of a pit 1,085m long, 650m wide and 230m deep. The lowest bench will be at an elevation of 309.5m above sea level. The in-pit haulage roads will be 24m wide.
Iron ore pre-treatment equipment. The pre-treatment stage of iron ore mainly includes crushing, screening, grinding, and grading processes.. Crushing and screening: The raw ore is sent to the crusher by the vibrating feeder, and the crushed product enters the screening machine. The materials on the screening return to the …
Iron ore crushing. 06-22-21; 495 Views; icon 0; At present, the jaw crusher and hammer fine crusher are widely used in the country for iron ore crushing. After the hammer crusher is crushed, the dry separation …
Image courtesy of Rio Tinto Iron Ore. Channar iron ore mine is situated 17km south-east of Paraburdoo mine in the province of Pilbara, a region in Western Australia. It is 60% owned by Rio Tinto Iron Ore and 40% by Chinese mining company Sinosteel. Rio Tinto Iron Ore operates the mine.
In October 2020, Australian gold mining company MACA has secured a A$185m ($131m) mining and crushing contract for the Fenix Resources' Iron Ridge iron ore project. As part of the six-year contract, MACA is responsible for drilling and blasting, mining, as well as crushing and screening works at the Iron Ridge project.
Environmental impact due to iron ore mining in Chhattisgarh. 2014 •. Dr. Bhumika Das. Iron ore is an important mineral in Chhattisgarh. The production of iron ore is 5.50 million tones per year. Due to massive extraction of iron ore, it pollutes air, water and soil. When iron in solution reaches the water table it pollutes the ground water ...
Iron ore - Crush+Size's double roll crusher crushes magnetite with a compressive strength of 300Mpa. Skip to content +49 (0) 2261 80 47 300 [email protected] Karriere / Careers. Crush + Size Technology & Co. KG. ... Redefining roller crushing technology – exploring limits – setting new standards ...
The iron ore is evenly fed by TSW1139 feeder into HJ98 high-efficiency jaw crusher for coarse crushing. After that, the materials would be sent into CS160 cone crusher for secondary crushing. Then the qualified materials enter into the 3YA1860 for screening while the return materials starts the secondary crushing with materials of 0-15mm,15 ...
Application field of iron ore crushing material. Iron ore is deeply processed by the crusher and can be widely used in the following industries. 1. Treat pig iron. Pig iron smelting adopts the high-temperature solid-state reduction method, that is, it is smelted under the condition that the furnace temperature is increased to 1150-1300 °C.
This paper presents an economic analysis of a mine-to-crusher model to estimate and minimize the operating expenses of an open-pit iron mine located in northern Brazil. The activities at this …
A total of 6 parallel lines process 9500 t/h of ore. Screening equipment is installed after the primary crusher, after the scrubber and after the tertiary comminution stage to separate the iron ore into a dry coarse fraction (8 – 40 mm) and a wet fine fraction (> 1 – < 8 mm). The fraction < 1 mm passes through another washing stage.
Bayan Obo is rich in iron, rare earth, niobium and other metals. Iron is one of the main minerals here. Iron is harder than most stones. According to the traditional iron ore processing process, the jaw crusher is used for rough crushing, and the ore is subjected to primary rolling from large pieces to small pieces.
The subcontractor SJ Crushing was hired to process the material for the Australian ore producer. The mine is located in the Kimberley Region in Western Australia and covers an area of 0.6 km² The complete plant consists of 4 Kleemann machines connected in series. 1 x jaw crusher MC 125 Z and 3 x cone crushers MCO 13 S
The iron ore impact crusher utilizes a plate hammer on a high-speed moving rotor to produce a high-speed impact on the iron ore fed into the crushing chamber. …
1. Introduction. Crushing plays an important role in the process of mineral processing. It consumes a large amount of energy and has a decisive influence on the downstream processing (Wang et al., 2012).High voltage pulses are a new type of crushing method, which has found wide range applications in the field of mineral processing due …
In this study, the crushing process of spherical iron ore particles, constructed by an Apollonian sphere packing (ASP) method, was numerically reproduced in a cone crusher by DEM. Firstly, the physical properties of iron ore particles were …
Six steps to process iron ore. 1. Screening. We recommend that you begin by screening the iron ore to separate fine particles below the crusher's CSS before the crushing stage. A static screen is used to divert the fine particles for crushing. This step prevents overloading the crusher and increases its efficiency.
Where HPGR technology has replaced traditional methods of crushing and grinding (e.g. SAG or ball mills), it has: Provided excellent throughput capacity and energy efficiency. Decreased energy consumption by up to 40%. Substantially reduced water consumption. Reduced recirculation and wear within crushing and grinding circuits.
Technology [1]. Samples of regular geometry have been tested for uniaxial and triaxial compression [2]; iron ore samples of arbitrary geometry have been tested in a laboratory ... Technological cycle of iron ore crushing and grinding under production conditions is possible only in terms of mechanical load being rather labour-consuming and energy-
McLanahan Mineral Sizers are designed to process a variety of materials, including copper, iron ore, gold, nickel, lithium/spodumene, coal, potash, phosphate and other hard rock and soft, non-coal minerals. They can be used in primary or secondary crushing applications. They excel at handling feeds with clays and other contaminants that are ...
حقوق النشر © 2024.Artom كل الحقوق محفوظة.خريطة الموقع