Green Sand Formula
To makegreen sand or like it also called molding sand (foundry sand) we need 3 ingredients: sand, clay and water.
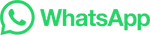
To makegreen sand or like it also called molding sand (foundry sand) we need 3 ingredients: sand, clay and water.
10. 5. Facing sand: Facing sand is the sand which covers the pattern all around it. The remaining box is filled with ordinary floor sand. Facing sand forms the face of the mould and comes in direct contact with the molten metal when it is poured. High strength and refractoriness are required for this sand. It is made of silica sand and clay …
9. How much time is taken by sand, for sand preparation in terms of muller time? a) 33 to 50 percent of muller time. b) 14 to 29 percent of muller time. c) 25 to 40 percent of muller time. d) 46 to 62 percent of muller time. View Answer. 10. Air blasts are provided for forced cooling of sand after muller operation.
Whereas synthetic molding sands are prepared artificially using basic sand molding constituents (silica sand in 85-91%, binder 6-11%, water or moisture content 2-8%) and other additives in proper …
Moulding sand is a special material used in foundry operations to create moulds & cores for metal casting. Learn types, constituents & properties of moulding sand. ... each property influences the behaviour of the sand during mould preparation, metal pouring, and solidification. This blog shall enumerate the different Properties of …
The first step in the sand casting process involves fabricating the foundry pattern – the replica of the exterior of the casting – for the mold. These patterns are often made from materials such as …
A process for preparing a molding sand for a green sand mold is provided. The process comprises the step of drying under a reduced pressure of 0 to 0.3 atm for 0.5 to 30 seconds a green molding sand obtained by kneading silica sand, clay, and water, to dry the clay superficial part and to retain in a moist state the clay deeper part on the silica sand core …
After cooling, the casting is separated from the mould and the green sand can be re-used. The three most popular automated moulding technologies for green sand casting are vertical, matchplate and horizontal flask moulding. Vertical moulding is predominately used for high volume, high precision casting due to its excellent efficiency and accuracy.
Step2: Mold Preparation. Purpose: Creating a mold using various types of sand, additives, binders, and water. Types: Hand molding and machine molding. Sand Types: Facing sand, system sand, green sand, dry sand, parting sand, loam sand, core …
System sand is used to fill the whole molding flask. In mechanical sand preparation and handling units, facing sand is not used. The used sand is cleaned and re-activated by the addition of water and special additives. This is known as system sand. Since the whole mold is made of this system sand, the properties such as strength, …
Preparation of moulding sand is a key process, determining the final quality of casting products. Special require-ments are imposed at stabilising and optimising the parameters of the moulding sand so that it should maintain its properties required for moulding. These requirements can be satisfied as long as specialised mixing systems are used
Moulding sand may be classified basically into two different types according to the type of base sand used; the natural moulding sand and the synthetic moulding sand [4, 5, 6]. Moulding sand for high and low …
Sand moulds were preferred to permanent mould due to several technical benefits, such as low process and raw materials cost, ease of mould making, minimized constraints on part geometry ...
It is a better moulding sand as its properties can be easily controlled by varying the mixture content. Composition of green synthetic sand for steel castings is as under. New silica sand — 25%, old sand — 70%, Bentonite — 1.5%, Dextrine — 0.25%, and moisture — 3 to 3.5%. Composition of dry synthetic sand for steel castings is as under.
Cascade Die Casting Expanding. Basic Principles of Sand Mixing. Sand, resin temperatures Time, speed, thickness, power Best design is …. Uniform dispersion needed Helix speeds Two resin-flow controls Calibrate regularly Potential problems. Mixing of any material or combination of materials is accomplished by moving the materials …
1. Experiment 2 Objective: To prepare a green sand mould for the solid, split pattern TOOLS REQUIRED: Moulding board, moulding box, rammer, trowel, lifter, gate cutter, riser, runner, sprue …
Sand preparation processes must be expertly conceived & conducted to permit reliable, cost-effective and environment-friendly manufacturing. The sand quality achieved depends on the specific processing technologies used. ... Meeting highest standards for moulding sand properties, casting precision and environmental protection. ...
mould for a split pattern. Place the bottom half of the split pattern on a flat moulding board, with the parting surface facing downwards. Sprinkle some parting sand on the pattern and the moulding board. Parting sand is silica sand without any clay or binding material. Then place a moulding box to enclose the pattern.
Core sand should be stronger than the moulding sand. 3.2 Properties of Moulding Sand. Moulding sand must possess the following properties to produce good moulds and castings. Refractoriness Moulding sand must not fuse when it comes in contact with molten metal. As the mould should withstand the molten metal temperature while it is …
The various types of moulding sand are. 1. Green sand 2. Dry sand 3. Loam sand 4. Parting sand 5. Facing sand 6. ... →In mechanical sand preparation and handling units, facing sand is not used. The sand which is used is cleaned and reactivated by adding of water, binder and special additives. And the sand we get through this is …
Shell molding is used for making production quantities of castings that range in weight from a few ounces to approximately 180 kg (400 lb), in both ferrous and nonferrous metals. This article lists the limitations or disadvantages of shell mold casting. It describes the two methods for preparation of resin-sand mixture for shell molding, namely ...
Dry Sand. The kind of green sand that has removed moisture is dry sand. In a good oven, the mould created from the green sand is baked or dried to create dry sand. Clay and silica make about 15% to 20% of the dry sand's composition. This Moulding sand is stronger, more thermally stable, and more rigid.
If a sand of suitable property is chosen, than it greatly minimises the casting defects that may be produced during the mould preparation and casting. In this blog we will discuss all the properties of moulding sand that it must possesses for the preparation of excellent mould. Properties of Moulding Sand A moulding sand should possess the ...
Preparation of molding sand and core sand. For modeling. Generally, a sand mixer is used to mix the old soil and the appropriate amount of clay. Molding. Make molds and core boxes according to parts drawings. Generally, a single piece can be made of wood molds. And mass production can be used to make plastic molds or metal molds.
5.03.6.8.2 Sand Preparation. Molding sand is prepared in a screw mixer if organic binders are to be used. Binder preparations are added to the sand and the mixer evenly distributes the resin over the sand grains. Samples are taken and tested for …
Molding sand is prepared in a screw mixer if organic binders are to be used. Binder preparations are added to the sand and the mixer evenly distributes the resin over the …
Foundry Questions and Answers – Moulding Sand Preparation and Conditioning. This set of Foundry Question Bank focuses on "Moulding Sand Preparation and Conditioning". 1. In the following equation, P stands for _____ ... Explanation: The measurement of the strength of molding sands can be carried out on the universal sand strength can be ...
2. Molding Sand. Molding sand is the sand that is used in the sand foundry process. It is typically made from silica sand, mixed with water and other additives to create a mold …
Green sand moulding is a traditional and widely used foundry process that forms the backbone of metal casting operations. It involves the creation of moulds using a mixture of silica sand, water, and a clay binder, giving it a greenish hue and earning its name. When compacted around a pattern, the green sand mixture retains its shape and …
A mould should possess appropriate permeability to enable escape of the gas evolved from the sand during the solidification of an alloy; the permeability is controlled during sand preparation. A mould should possess sufficient flexibility to control the stresses and shrinkage on solidification.
حقوق النشر © 2024.Artom كل الحقوق محفوظة.خريطة الموقع