The six main steps of iron ore processing
Six steps to process iron ore. 1. Screening. We recommend that you begin by screening the iron ore to separate fine particles below the crusher's CSS before the crushing stage. A static screen is used to divert the fine particles for crushing. This step prevents overloading the crusher and increases its efficiency.
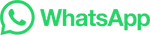