Review on vertical roller mill in cement industry & its …
Vertical roller mill has proved to be a popular choice for finished cement grinding over all other machineries due to advantages like low power consumption, …
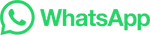
Vertical roller mill has proved to be a popular choice for finished cement grinding over all other machineries due to advantages like low power consumption, …
The reliable and energy-saving grinding system. For new plants, the polycom® is an economically superior concept compared to conventional systems. The polycom® is also predestined as extension investment to achieve maximum throughput increases of existing plants. With its low space requirement and the high capacity in relation to machine size ...
Vertical roller mill and roller press are two popular cement grinding machines. The two equipments are different in grinding mechanism, structure design, and product performance, but each has its own …
The cement industry is the main supplier of raw materials for the production of concrete and reinforced concrete. For grinding cement, two types of mills are used - ball and roller.
Taking grinding P · o42.5 cement as an example, the pre grinding closed-loop system composed of roller press or external circulation vertical mill and powder concentrator has a circulation load rate of 200% – 300%, …
Cement grinding with our highly efficient ball mill. An inefficient ball mill is a major expense and could even cost you product quality. The best ball mills enable you to achieve the desired fineness quickly and efficiently, with minimum energy expenditure and low maintenance. With more than 4000 references worldwide, the FL ball mill is ...
What Is Raymond Mill. Raymond mill is also called Raymond roller mill. It is a new type of high-fineness grinding mill with high efficiency and closed circulation, which can completely replace the cement ball mill.This kind of machine is commonly used in cement plants for raw materials fine grinding, such as limestone, coal, gypsum, etc. Under normal …
March 21, 2024. By. admin. Cement EXPO 2025, which will be held along with the 10th Indian Cement Review Conference and the 8th Indian Cement Review Awards, promises to be bigger, drawing in greater participation, fostering more profound discussions and showcasing the continued evolution of the cement industry. Mumbai.
The cement roller press is a type of material-crushing machine which is often used in cement plants. It usually works together with a ball mill to form a pre-grinding or final-grinding system for the grinding of raw materials, coal, and clinker.. Compared with the traditional tube mill and ball mill, the roller press has lower energy consumption and …
Clinker size is important for the optimization of cement grinding, and is also an indicator of cement quality. Having a high percentage of coarse clinker can be difficult to grind. ... Fine clinker is more of an issue in vertical roller mills, since it can quickly slip under the rollers, leading to vibration and instability. As a general rule ...
A compact coal mill solution for grinding virtually any type of raw coal. Our ATOX® Coal Mill is a compact vertical roller mill that can grind almost any type of raw coal. The coal mill utilises compression and shear force generated between the large rollers and the rotating table to crush and grind raw coal, removing the need for a separate ...
Abstract. Grinding is an essential operation in cement production given that it permits to obtain fine powder which reacts quickly with water, sets in few hours and hardens over a period of weeks ...
38]. Various grinding laws, energy relationships, control factors and controller design for cement grinding are discussed in [37]. Figure-1. Vertical roller mill for cement grinding [13]. VRM shown in Figure-1 uses hydraulically hard-pressed conical shape 2-4 rollers against the horizontal revolving grinding table. To enhance comminution, the
1. 2. Roller diameter: 1400~2000 mm. Production Capacity: 950~1050 t/h. Application: raw material of cement, clinker and etc. get price! The cement roller press, also known as roller press in cement plant, high pressure grinding roll (HPGR), is a kind of cement equipment for brittle materials, apply for grinding cement clinker, cement raw ...
Simply put, the roller press is the most energy-efficient grinding machine on the market. Since its commercial introduction into the cement industry by KHD in the 1980s, hundreds of them have been installed in the cement and minerals industries, in both finish and semi-finish applications. And with the lowest specific energy consumption among comparable …
Output: 290–1580 t/h. Power: 2×250–2×1800 kW. Highlights: fully automatic, high efficiency, etc. GET QUOTATION. The cement roller press is a kind of grinding equipment applied for brittle materials, such as …
Roller press circuit in finish mode operation for Pozzolanic and composite cement is an emerging system which has a high potential for energy saving and ease of operation hence further possibilities to explore this circuit in grinding of mix aggregate or composite cement lead to a systematic approach towards eco-friendly efficient circuit.
Cement Grinding Plant / Grinding Unit. Output Capacity: 100 ~ 5,000 TPD. Grinding Mills: roller press / vertical roller mill / ball mill. Grinding Systems: open circuit / closed circuit / vrm final grinding. SEND INQUIRY. As a leading cement plant builder, AGICO offers an expert cement grinding plant EPC service.
Cement mixtures produced by separated-grinding in a vertical roller mill and a classic ball mill in the tkIS technical center (Fig. 1) will be verified with regard to cement properties according to DIN EN 196 and with …
See more on cementplantsupplier
The particle characters and their physical properties of vertical roller mill finish grinding cements were studied in this paper. The difference with roller press-ball mill combined grinding products was also analysis. The results were shown that the particle size of the vertical roller mill finish grinding cements was more evenly distributed at the …
Abstract. The particle characters and their physical properties of vertical roller mill finish grinding cements were studied in this paper. The difference with roller press-ball mill combined ...
Why install Roller Press in Cement Manufacturing Plant. The overall trend is to increase the capacity of pre-grinding bed, and transfer 60% to 70% of of the ball mill functions section to it and high fine airflow classification equipment to complete the system, with a large range of increased production and power saving capacity.
In conclusion, the application of vertical roller mill technology in the cement industry has revolutionized the way cement is produced. VRMs are more energy-efficient, eco-friendly, and produce a more consistent product compared to traditional grinding mills. They are also more suitable for use in urban areas due to their lower noise level.
Comflex grinding system from KHD consumes less energy compared to other similar process circuits and is a proven fact for raw material, slag grinding and composite cement grinding. The ambition to save energy during the production leads to the deeper investigation to grinding cement in finish mode with roller presses also.
Abstract. This work concentrates on the energy consumption and grinding energy efficiency of a laboratory vertical roller mill (VRM) under various operating parameters. For design of experiments (DOE), …
Smart vertical roller mill design for raw, cement and slag grinding. The OK™ Mill was originally designed for cement grinding. In 2017 we released the OK™ vertical roller mill for raw materials grinding. The OK™ Mill's modular design comes with unique flexibility, showcasing parts commonality, where spare parts can be shared between ...
For a ball mill grinding OPC to a fineness of 3200 to 3600 cm2/g (Blaine) the cost of wear parts (ball, liners and mill internals) is typically 0.15-0.20 EUR per ton of cement. For an OK mill grinding a similar product, the cost of wear parts depends on the maintenance procedures, i.e. whether hardfacing is applied.
Grindability of a 95/5 OPC at various Blaine fineness: o 27-32 kWh/t at 3,000 cm²/g. o 39-47 kWh/t at 4,000 cm²/g. o 58-69 kWh/t at 5,000 cm²/g. Every 100 cm²/g increase in cement fineness increases the mill power …
حقوق النشر © 2024.Artom كل الحقوق محفوظة.خريطة الموقع