Model 4-F Hand Mill | Quaker City Grinding Mills
4-F Hand Mill Brochure. The original Quaker City Grinding Mill (QCG). Over 100 years in service. The F4 manual, disk grinding mill is used in fine testing labs around the world. The F4 mill head construction is made of …
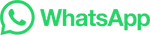