Mining & Mineral Processing Plant
Mainly including mineral (sand) mining and processing. The mineral sand beneficiation process is consisting of crushing – screening – washing – separation – dewatering and drying. JXSC provides conventional ore processing plant equipment suitable for your ore beneficiation plant site, high recovery rate up to 99.9%.
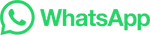