Iron ore beneficiation | Commodities | Mineral Technologies
We then deliver concept, pre-feasibility and feasibility studies as well as cost effective flowsheet design to safely and efficiently extract the iron ore. Innovative plant design Using the optimised flowsheet design, our engineering team will then develop a safe and effective processing plant specific for your ore body, aiming to extract high ...
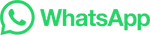