Direct Reduced Iron and its Production Processes – …
Iron ore is used mostly in pellet and/or lumpy form. Oxygen (O2) is removed from the iron ore by chemical reactions based on H2 and CO for the production of highly metalized DRI. In the direct reduction process, the solid metallic iron (Fe) is obtained directly from solid iron ore without subjecting the ore or the metal to fusion.
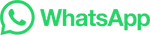