AERATED AUTOCLAVED CONCRETE (AAC) BLOCKS: …
IJARESM Volume I, Issue II 24 These voids are typically 1mm - 5mm across and give the characteristic appearance. compact. 4. Densities range from about 460 to 750 kg/ m3 Medium density concrete ...
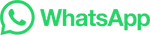
IJARESM Volume I, Issue II 24 These voids are typically 1mm - 5mm across and give the characteristic appearance. compact. 4. Densities range from about 460 to 750 kg/ m3 Medium density concrete ...
88. 3.5. Cement. Cement is one type of widely used hydraulic binding materials. The common portland cement is suitable for producing AAC. Common portland cement mainly includes CaO, SiO 2, Al2O 3, Fe 2 O 3 and small amount of MgO and SO 3. As the main calcium materials, cement can be used alone, but cement is more likely to be used with …
Autoclaved aerated concrete (AAC) is the lightest masonry material available in today's building industry. It shows properties, such as high strength per unit weight, lesser density, lower shrinkage, higher thermal insulation, and fire resistance as compared to traditional concrete. Not only engineering properties of AAC make it …
Gypsum is a very popular mineral additive used in autoclaved aerated concrete (AAC) technology. In many studies, tobermorite can be synthesized from calcium-silicate-hydrate (C-S-H) phase under hydrothermal conditions in the presence of gypsum, and its impact on the tobermorite content in the AAC blocks has been discussed.
The associated MgO in limestone is believed to affect the volume stability of cementitious materials at room temperature, which limits the utilization of low-grade …
Abstract. Lime is one of the main raw materials necessary for the production of autoclaved aerated concrete (AAC). The preparation of lime by calcining …
Vernor Material & Equipment has been in the business of selling earthen and road base materials since it was founded in 1958. We sell limestone base and rock of all sizes, crushed concrete, gravel, Rip Rap, sand, sand blast grit, lime, and cement. Click on any thumbnail to see larger pictures of the materials we provide.
Aerated concrete (AAC) or lightweight concrete is primarily used for non-load bearing structures in construction work. Generally, it is produced with cement as a main binding ingredient, and the production of cement is blamed to contribute 7 to 8% of CO2 emission in the environment. In addition, the dumping of industrial wastes is also a …
Primary raw material used to manufacture AAC is fly ash. Fly ash (or pond ash) is an inert material and does notallow termites or other pests to survive. III. Advantages of using Autoclaved Aerated Concrete 1.12. Lightweight AAC blocks are about 50% lighter than clay bricks of equivalent size. This translates into less dead weight of
The lightest masonry material available in today's market is AAC blocks (Autoclaved Aerated Concrete Blocks) whose density is about 1/3 rd times of the clay bricks and fly ash bricks and about 1/5 th times of the Concrete because of its -like structure made up of 80% of air voids while they are being used since the 1920s in most of the part in Europe …
This paper describes the behavior of phase change materials that are inbuilt in aerated concrete blocks. Two building samples of an aerated concrete wall were measured in laboratory equipment ...
In this context, an effective strategy to be pursued is represented by the use of construction materials with enhanced thermal properties, together with a reduced …
Autoclaved Aerated Concrete as a building material exists and has been industrially produced since the beginning of 20th century. AAC stands for Autoclaved Aerated Concrete, otherwise known as Aerated Cellular Concrete or Aircrete. Early history of autoclaved aerated concrete is based on a series of process patents. In 1880 a German
The heat flow rate is: (3) Q = q A Therefore, the equation is recast as: (4) Q = − k A ∂ T ∂ x Concrete is a common material all over the world and more than ten billion tons of concrete are produced every year [14].It is expected that the demand for concrete will increase to 18 billion tones by 2050 [15].Concrete is widely used in buildings, …
The air entrained concrete takes in the air of 3 to 8 percent. It also differs from the retarded mortar and aerated concrete for the same reason of percentage of air entrained. In the case of retarded mortar systems, it is 15 to 22 percent. The bubbles are chemically formed in the case of an aerated concrete. History of Concrete
Autoclaved aerated concrete, or AAC, was invented in Sweden in the early 1900s and patented in 1924. It is made by creating a slurry of finely ground quartz sand, calcined gypsum, lime and/or Portland cement, water, and a small amount of aluminum powder. The slurry is poured into rectangular tanks, filling them only partway.
Hebel ® AAC is 5 times lighter than traditional concrete, which not only has a significant impact on reducing construction time but cost savings are seen as well. Often Hebel ® can reduce the use of steel, concrete and …
The aluminum powder was added at 0.4% by weight of binder to introduce aeration in concrete. Before testing, samples of aerated concrete were cured with steam in an autoclaving machine for 9 h at a pressure and temperature of 1.5 bars and 127 °C respectively and oven-dried at a temperature of 105 °C for 24 h after steam curing.
Nowadays, Autoclaved Aerated Concrete (AAC) blocks are actively present in the marketplace by manufacturers like Hebel or Retak, which are building an easy to use and efficient constructive system ...
Autoclaved aerated concrete (AAC) blocks have widespread popularity in the construction industry. In addition to lightness, these materials have other advantages, including fire resistance, low …
Autoclaving converts the material to Tobermorite, a naturally occurring mineral found in limestone deposits whose crystal structure has some properties similar …
Aerated concrete (AC) is a popular building material which is used all over the world. It has a history of 50 successful years can be used in all environments for all types of buildings (W ittmann ...
1. Introduction. In the past century, research and production technology of autoclaved aerated concrete (AAC) have been constantly developed. With the feature of integrated performance in thermal insulation, fireproofing and durability, AAC becomes a green lightweight building material [1,2,3].In China, to meet the design standard of the …
An improved method for the manufacture of aerated concrete is proposed, which consists of introducing cement pre-hydrated for 20–30 min into the composition of the aerated concrete mixture and ...
1. Introduction. Aerated concrete is lightweight concrete that has been aerated. Aerated concrete is sometimes referred to as cellular concrete. It will be divided into 2 main varieties in keeping with the tactic of production [1], [2], [3], [4].AAC is made by mixing aluminum powder and various additives into a suspension of ground high silicon …
Raw materials used for producing autoclaved aerated concrete are fine grade materials. Fly ash or sand, lime, cement, water, and aluminum powder are the main raw materials for producing AAC. A total of 3150 kg of mixture (43–45% fly ash or sand, 36–38% water, 13–14% cement, 6–7% lime, and 0.025–0.03% aluminum powder by …
A brief report on. Autoclaved Aerated Concrete (AAC) products. By. Vishal Kansagra. AAC Project Report by Vishal Kansagra. Vishal@aac-india (+91) 98796 09129 2. Chapter-1: Introduction to Autoclaved Aerated Concrete (AAC) products Overview AAC was invented in mid-1923 in Sweden. It is also known as …
Autoclaved Aerated Concrete, also known as AAC or aircrete, is a green precast building material present in the global market for over 70 years and is extensively used in residential, commercial and industrial construction. AAC is a well-established building material, which has rapidly gained worldwide market share from conventional building ...
Their distinctive properties of durability and strength make them an ideal and cost-effect solution for all types of load-bearing walls. Dense aggregate concrete blocks are manufactured from cement, sand and aggregates. • Typical thermal conductivity: 0.70 – 1.28 W/mK. Durable. Reusable, particularly where lime mortars have been used.
Quicklime is key in the ing process, as it reacts immediately with cement, gypsum, water and aluminium powder when making aerated autoclaved concrete blocks. The ratio of Lime in the Mixture of making AAC blocks manufacture is: Fly Ash/Sand : Lime : Cement : Gypsum = 69 : 20 : 8 : 3. 3. Quick Lime for AAC Blocks.
حقوق النشر © 2024.Artom كل الحقوق محفوظة.خريطة الموقع