Research Progress on Low-Pressure Powder Injection …
Powder injection molding (PIM) is a well-known technique to manufacture net-shaped, complicated, macro or micro parts employing a wide range of materials and alloys. Depending on the pressure applied to inject the feedstock, this process can be separated into low-pressure (LPIM) and high-pressure (HPIM) injection molding. …
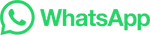