Baghouse in Cement Plants: Understanding How They Work …
Find out how cement baghouses work, the different types of dust collected, and some essential factors to keep mind to write up a proper inspection form. +1 (918) 406-5684. ... Baghouses come in different designs and specifications; however, the basic operation principle is the same for all types. Baghouses are made up of numerous bags that are ...
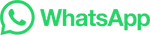