Beneficiation of Gold and Silver Ores | SpringerLink
These pebbles tend to be more resistant to impact breakage in the SAG mill, and crusher creates ore surfaces more conducive to breakage in the ... P.M. 1925. A mineralogical investigation of refractory gold ores and their beneficiation with special reference to arsenical ores. Journal South African Institute of Mining and Metallurgy 88 (5 …
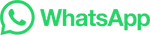