Focused high- and low-energy ion milling for TEM
The focused low-energy argon ion milling of the Ge 2 Sb 2 Te 5 material was done under liquid N 2 cooling. S/TEM observations were performed with a probe Cs-corrected Titan 3 G2 60–300 microscope equipped with high-angle annular dark-field (HAADF-), bright-field (BF-), ADF, annular BF-STEM and Super-X EDX detectors as well …
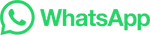