(PDF) Potential Processing Routes for Recovery of
nickel and copper; and the Platreef has lower PGM values, ... Crushing and. grinding (80% passing. 75 µm ) 4 L Flotation. cell (SIBX) CuSO. 4. pH 9. ... chromites, and silicates, fine grinding is ...
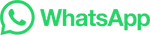