Use Cement Ball Mill Grinding Cement Clinker | Cement Ball Mill Operation
The cement ball mill operation is more practical and the energy-saving effect is better. In terms of production capacity, the output of cement ball mill produced by us can be increased by 15% – 20% compared with the one made by other cement ball mill manufacturers, while the power consumption is reduced by 10%. ...
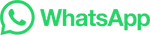