(PDF) DESIGN AND OPERATIONS CHALLENGES OF A SINGLE TOGGLE JAW CRUSHER
A review on the design and operations challenges of a single toggle jaw crusher is presented. Strength and fracture toughness of the material to be crushed are intrinsic properties that determine ...
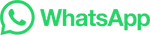