Iron processing
The partially reduced ore is then smelted in the second unit, and liquid iron is produced. Smelting-reduction technology enables a wide range of coals to be used for iron making. Iron processing - Ores, Smelting, Refining: Iron ores occur in igneous, metamorphic (transformed), or sedimentary rocks in a variety of geologic environments.
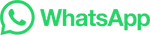