How Cement is Made | CEMEX UAE
This process takes place in silos equipped for obtaining a homogenous mix of the material. 8. Calcination . Calcination is the core portion of the process, in which huge rotary kilns come into play. Inside, at 1400 degrees C, the raw material is transformed into clinker: small, dark gray nodules 3-4 centimeters in diameter. 9. Cement milling
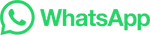