Advanced Analytics for Mineral Processing
Mineral processing is a field that contends with procedures and technologies used for separating valuable minerals from gangue or waste rock. It is a process that ... combination of ball and rod mills is used to reduce the size during grinding further. Steel balls with diameters ranging from 1 to 10 cm are used as the grinding media
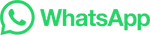