Ball & Rod Mill Density
Rod mill grinding efficiencies have been shown to increase in the range of 5 to 15% with more dilute discharge slurry (i.e., increased feed water) at least down to the range of 45 to 50% solids by volume. The higher the discharge % solids in the plant rod mill, the better the candidate for feed water addition rate test work.
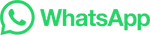