design specifications of ball mill liners
Specifications of a ball mill liner A ball mill liner has an anti-pulp racing design to avoid the pulp circulating. It is also designed to minimize the consumption of the grinding media. The choice of alloy that is used for the liner depends on …
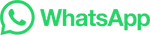