Construction of Ball Mill | Henan Deya Machinery Co., Ltd.
A concept which has found some application for ball mills is the "angular spiral lining". The circular cross-section of a conventional mill is changed to a square cross-section with rounded corners by the addition of rubber-lined, flanged frames, which are offset to spiral in a direction opposite to the mill rotation.
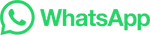