Clinker grinding technology in cement manufacturing
Clinker grinding technology is the most energy-intensive process in cement manufacturing. Traditionally, it was treated as "low on technology" and "high on energy" as grinding circuits use more than 60 per cent of total energy consumed and account for most of the manufacturing cost. Since the increasing energy cost started burning the benefits …
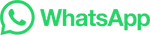