Cement Mill Optimization: Practical Strategies for …
Cement mills are critical components in the cement manufacturing process, responsible for grinding raw materials into fine powder to produce cement. Optimizing the operation of cement mills is essential to …
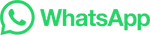