Filtration and Separation In Sulfur Recovery
(Page 1) Sulfur is a major contaminant in the oil and gas industry that exists in various forms and requires separation from both water and process streams. In the many plants that make up the sulfur recovery trail, filtration and other separation processes are important in minimizing process upsets caused by the presence of contaminants. In fact, …
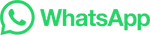