Crushers
Jaw crushers, gyratory crushers, and cone operate according to the compression principle. Impact crushers, in turn, utilize the impact principle. Jaw crushers . Jaw crushers are mainly used as primary crushers. Their main purpose is to reduce the material to a small enough size that it can be transported by conveyors to the next …
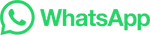