STAL Technology Brings Green Nickel into Reality
While HPAL technology has processing capacity up to 35,000 tons per year, STAL technology requires only 1,800 tons processing capacity per year. Given the fact that most of nickel miners in these regions are small-to-medium scale miners, Widodo proposes these IUP holders with close proximity in the same region to collaborate in developing …
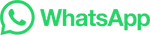