Clinker formation process in a modern plant rotary kiln.
Cement production in rotary kilns requires large amounts of thermal energy, which is provided by combustion of different fuels. Substitution of fossil fuels by refuse derived fuels (RDF) can ...
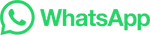