Crushing it: A Comprehensive Guide to Stone Crusher Plants
A stone crusher plant is a machine designed to reduce the size of large rocks, eliminate gravel, or rock dust to smaller sizes for various applications. These …
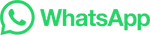
A stone crusher plant is a machine designed to reduce the size of large rocks, eliminate gravel, or rock dust to smaller sizes for various applications. These …
Designed to fill the gap left in the market by cone and jaw crushers, horizontal impact crushers are ideally suited for contaminated materials and can easily handle any clay, dirt or metal mixed in with the …
A stone crushing plant needs essential primary crushers like jaw and gyratory crushers as well as fine-crushing equipment like impact crushers and ball …
Typically, the minimum setting on most primary crushers will be about 4 to 6 inches, as noted above. Compression-style jaw, cone, impact crushers, and gyratory crushers are most often appropriate as primary crushing equipment types, though there can be overlap between primary and secondary crushers as far as suitable types. 2. Secondary Crushing.
Cement mill is another necessary cement equipment of the cement plant. After raw material crushing, cement mill plays vital role in the further cement manufacturing process. Cement ball mill, vertical cement mill, and cement roller press are common types of cement grinding plant. cement ball mill. Cement mill has two functions of the cement ...
GB401 - Large Glass bottle crusher. GB401 glass bottle crusher is a multi-feed crushing machine and can accept a large number of glass bottles. It can crush 50-100 glass bottles in 1 minute. We can customize cutters and spacers for effective crushing force. After crushing, the glass bottle fragments are about 10-50 mm.
Secondary crushing is the second stage of crushing that takes place after the primary crushing. The secondary crusher is the equipment that reduces the size of the materials further, after they have been reduced by the primary crusher. The secondary crusher has a size reduction ratio ranging from 3:1 to 5:1. The secondary crusher can …
Crush material in a metallurgical plant : ORIGINATOR: SGB Mining and Minerals : PRIMARY OR DELEGATED QUALITY ASSURANCE FUNCTIONARY - FIELD: ... The learner will be required to crush material by means of one or more of the following equipment units: Cone-type crusher. Impact-type crusher. Jaw crusher.
There are three main steps in designing a good crushing plant: process design, equipment selection, and layout. The first two are dictated by production requirements …
Let's clear what stone crusher plant actually does. "Stone crusher plant is a machine designed to reduce the large stone, granites, marble, lime rocks into the smaller size and output gravel, dust, different size of the material.". Stone crusher plants used worldwide. It is available with different-2 capacity, design, and utility.
stone jaw crusher price: $9800~$210000. stone cone crusher price: $26000~$450000. stone Impact crusher price: $19000~$68000. If you want to buy a mobile crusher, the mobile stone crusher machine price is a little higher. The price ranges are: Wheeled portable stone crusher machine for sale: $550000-$1350000.
The machines involved in this process, such as crushers, screeners, feeders, and conveyors, work together to ensure that the final product is of the required size, shape, and quality. This equipment is essential for creating high-quality construction projects, from roads and bridges to buildings and other structures.
Jaw Crushers. Jaw crushers are the most commonly used crushed stone machines. They have a simple design and are suitable for handling a wide range of materials, including hard and abrasive materials. Gyratory Crushers. Gyratory crushers are larger crushed stone machines that are used to crush large rocks into smaller pieces.
Vess Machine produces crushing and screening plants suitable for any project. we design the crushers based on your input stone size, type, and the required sizes in output. We produce our crushing and screening plants in different capacities suitable for mountain and river material. An automatic washing system can be applied to …
Mobile crushers are track-mounted rock crushing machines that are easily movable on and between production sites. They are widely used in aggregates production, recycling applications, and in mining operations. Mobile crushers can replace stationary crushing systems, which reduces the need for hauling and thus cuts operational costs. Versatility.
Crusher: The crusher is the main component of the mobile crushing plant. It crushes the material into smaller pieces, reducing them to a size that can be transported by conveyors or other means. Conveyor: The conveyor is used to transport the crushed material to a designated area for further processing or stockpiling.
If you need a high quality wood crushing machine, please feel free to contact us. Model: SL-80. Capacity (kg/h): 1.5-2t. Motor (kw): 37. Cyclone diameter (m): 1. Hammers (pcs): 50. Wood crusher machine is a mechanical device used to reduce the size of wood materials into smaller pieces.
Feeder – A feeder machine is included in a feeder crushing plant, a type of mobile or permanent crushing plant, to control the flow of raw materials into the primary …
Introduction. An aggregate crushing plant is a machine that processes a wide range of raw materials into high-quality aggregate, which is used in a variety of construction applications such as roads, …
Safety Tips. When working with plastic crusher machines, it is crucial to follow safety procedures, including: Always keep hands away from the moving parts of the machine, especially during operation 3. Wear proper …
200 tph Stationary Crushing Machine in The Philippines Quarry. The clients had relatively high requirements for aggregate particle size. Thus, the production line is with high output capacity of about 200 t/h. Here are the details about the quarry crushing plant as follows: Capacity: 200 t/h. Crushing material: granite.
Learn everything you need to know about primary crushing, secondary crushing, and tertiary crushing in this comprehensive guide. Discover the types of crushers used in each stage, their working …
Handbook of Conveying and Handling of Particulate Solids. G. Lodewijks, ... A. Newman, in Handbook of Powder Technology, 2001 2.1 The primary crusher. The primary crusher is located in the quarry and consists of a McLanahan 48″x72′ Shale King Crusher rated at 1,000 TPH (Tons Per Hour). The driving flywheel has a diameter of 2.5 meters and is …
A well-designed plant layout balances the capital versus operating cost over mine life. Buildings, infrastructure, and major equipment items, represent the major cost elements of a crushing plant. Yeco …
The limestone crushing plant is mainly composed of vibrating feeder, jaw crusher, impact crusher, cone crusher, circular vibrating screen, etc. To meet the different requirements of customers' needs, it can be equipped with sand making machines, dust removal equipment, sand washing machines, etc.
Stone crusher plantdesign is a crucial factor in the efficient operation of the crushing process. The primary goal of plant design is to achieve the desired product size and capacity while balancing capital and operational costs. A well-designed plant will help minimize production downtime and … See more
Table Source: Wikipedia (Crushers) Cone crushers use a spinning cone that gyrates in the bowl in an eccentric motion to crush the rock between the cone surface, referred to as the mantle, and the crusher bowl liner.Gyratory crushers are very similar to cone crushers, but have a steeper cone slope and a concave bowl surface. As the gap …
The raw material storage area stores large boulders and rocks for processing in the stone crusher machine plant. Vibrating feeder. The vibrating feeder delivers the raw materials to be crushed to the crusher. Then it ensures that raw materials flow into the crushing chamber at the required speed and flow. Primary crusher
Step 1: Turn Large stones into small stones. Transport the bulk dolomite raw material into the jaw crusher by the vibrating feeder for the coarse crushing process, and then send it to the cone crusher for medium to fine crushing processing until it reaches the feed fineness of the grinding machine (15-40mm) before discharge.. Step 2: Grind small …
The process ensures the production of high-quality materials suitable for use in different building projects. The versatility and reliability of the mobile crusher plant make it an ideal choice for meeting diverse construction material requirements. Raw materials used: maximum 600mm. Finished particle size: sand between 0-24mm.
حقوق النشر © 2024.Artom كل الحقوق محفوظة.خريطة الموقع