An overview of energy savings measures for cement industries
The current global consumption of cement industry is about 1.5 billion tons per annum and is rising at almost 1% per annum. Cement production requires approximately 110 kW h/t of electrical energy, with 40% directed to clinker grinding [26].Using real auditing, Avami and Sattari [17] investigated technological methods that …
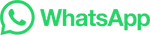