4.3: Piping and Instrumentation Diagrams
A Piping & Instrumentation Diagram (P&ID) is a schematic layout of a plant that displays the units to be used, the pipes connecting these units, and the sensors and control valves. Standard structures …
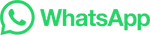
A Piping & Instrumentation Diagram (P&ID) is a schematic layout of a plant that displays the units to be used, the pipes connecting these units, and the sensors and control valves. Standard structures …
Additionally, chemical injection is used to mitigate the formation of scale and prevent corrosion in pipelines, thus extending their lifespan and maintaining productivity. 2. Water Treatment: One of the most critical applications of chemical injection is in water treatment facilities. Chemicals like chlorine, ozone, and coagulants are added to ...
As presented below, the optimization of pipe diameters can be accomplished using equations that relate the recommended velocity of fluids and the cost of energy. To determine the recommended velocities and compare what was published 10 years ago [ 1] to 2017, Equation (1) is used (Table 1, top). It is presented in Ref. 2.
ASME B31.3 specifies the minimum requirements for materials, design, fabrication, testing, and inspection of process piping systems. It covers a wide range of topics, including pipe sizing, pressure …
hydrostatic testing. pipeline separation services. pipeline chemical cleaning. gas flaring. pipeline drying. line commissioning and decommissioning. Advanced technologies. We …
Welcome to Chemical Process Piping! A company that has been making. India self-reliant since 1964. We are one of the largest in the field of design, manufacture, and installation of FRP/GRP, GRE, and thermoplastic lined …
2.1 Basic principles of chemical process technology. ... Pipe Racks: Provide a way of organizing interconnecting pipes and cables between different areas/units of process plants. Pipe racks are either single or multilevel structural steel members usually spaced 20 ft apart. The width of the rack is dependent upon the number of pipes and cables ...
Question: FIGURE Q21 shows a chemical process pipeline, surrounded with insulation material in order to keep the product inside at a constant temperature and to avoid energy loss to the surrounding. Two Type ) thermocouples are used to monitor the temperature of the pipeline, T, and the temperature of the outer insulation wall, T. FIGURE Q21 ...
P + ½ mV 2 + ρgH = K where P is pressure, m is mass, V is velocity, ρ is density, g is the gravitational constant, H is height, and K is a constant. Thus, when velocity drops in the splitting manifold, something else must change. For a simple system, ρ, g and H do not change, so P must.
Process Chemical. Chemical Processing facilities present many challenges for labeling with their inherently harsh environments, diverse site-specific production processes, and extremely complex piping systems. We offer pipe labels, plant signage, and equipment tags that are specifically designed to withstand harsh conditions.
Pipeline Cleaning. Chapter. First Online: 13 February 2021. pp 13–20. Cite this chapter. Download book PDF. Download book EPUB. Technology Standard of Pipe …
One regular factor in flow rate design is the calculation of pipe size. To diminish capital cost, some engineers may decrease the pipe size and increase the velocity. ... Chemical/process engineering design, Agile project management, Process economy and optimization and other related courses will also be added into course agenda of …
Pipeline and process chemical solutions. SureGL™ pipeline gel solutions. SureGL™ gel systems provide unique solutions for pre-commissioning, flow assurance and decommissioning of pipelines and …
The latter three comprise most of the chemical process industry single-unit control problems. P&IDs have a number of important uses in the design and successful operation of chemical process plants. Once a process flow diagram is made, P&IDs help engineers develop control strategies that ensure production targets are met while …
PIPING SYSTEMS. PDFL offers a comprehensive range of solutions to meet your growing demands in fabricating water and wastewater pipe systems, process pipework, stainless aeration systems, and PVC/ABS dosing systems. We are the world's leading suppliers of piping products offering pipework design, manufacture, and installation of all pipework ...
The transportation and storage of fluids is a key variable in the design and optimization of a chemical process facility. The major components involved in this step of process design are the piping, …
20 April '23. Pipeline Corrosion occurs when a pipeline's material begins to deteriorate or weaken over time, due to chemical reactions with its surroundings. Corrosion is a significant challenge faced by industries that use process equipment and pipelines. Failure to manage corrosion can lead to leaks, explosions, and costly downtime.
Blasting also removes any mill scale that has accumulated at weld locations during the pipe fabrication process. Chemical Cleaning. Hot Water. Piping systems that convey dry, powder-like materials must be free of oil or grease. Otherwise, the conveyed material could build up within the piping during operation, altering material flow rates.
The chemical agents and the dirt in the pipeline undergo physical and chemical reactions to dissolve the dirt in the pipe. This technology is used for cleaning by physical methods that are difficult to remove or for pipes of special shapes. 2. Chemical cleaning process: injection pumps, chemical tanks and other equipment are in place, …
A successful cleaning chemical formulation process for hydrocarbon transportation pipelines has been developed and applied in pipelines in the U.S. Case studies are included in this article. ... The lessons learned from the case histories are: 1) the specialty pipeline cleaning chemicals showed high efficacy of treatment, 2) solids removal was ...
Pipeline and Process. Explore our pipeline and process services. Diagnostics. Visual, pressure-wave and chemical analysis driving customized solutions design. Explore. …
Optimize chemical reactions with BIOVIA Pipeline Pilot: leverage Bayesian Optimization, EDBO+ Python package, and BIOVIA Notebook ELN. No coding expertise needed. Discover efficient workflow for enhanced yield. ... A solution is to use BIOVIA Pipeline Pilot 8 to extract and process data from the BIOVIA Notebook 9 ELN, run the …
Pipeline pigging is the process of using a specialized device called a "pig" to clean, inspect, and maintain pipelines used for transporting liquids or gases. Pigs are typically made of various materials, such as rubber, urethane, or steel, and are inserted into the pipeline through access points called "pig launchers" and "pig ...
Sizing. Since pipes can come in a variety of shapes and sizes, the specifications also define the proper sizing of a pipe marking. The size of a pipe marking label is set based on the pipe diameter as follows: ¾ – 1 ¼" = at least 8" in length and ½" in height. 1 ½ – 2" = at least 8" in length and ¾" in height.
The pipeline is typically isolated and the cleaning equipment is inserted into the pipeline. The cleaning process may involve multiple passes with the equipment, and may also involve the use of chemicals or other cleaning agents. Inspection: After the cleaning process is complete, the pipeline is inspected again to ensure that all debris has ...
Description. ASME has been defining piping safety since 1922. ASME B31.3 contains requirements for piping typically found in petroleum refineries; chemical, pharmaceutical, hydrogen, textile, paper and pulp, power generation, semiconductor, and cryogenic plants; and related processing plants and terminals. It covers materials and components ...
Pipeline corrosion may occur externally and/or internally, and both mechanisms take place due to the presence of water in the environment. Corrosion in aqueous solutions is the most common corrosion process observed. In terms of internal corrosion, the water may be present as contaminant in several process streams.
When it comes to ensuring the coating will bond properly to the pipe wall, surface preparation is the most critical factor. The in-situ coating process involves two separate methods of cleaning the pipe wall: abrasive blasting and chemical cleaning. Learn about both methods today.
Pipeline cleaning refers to the process of removing contaminants and debris from the inside of pipelines that are used to transport fluids such as water, oil, and gas. Over time, pipelines can accumulate sediment, …
One such maintenance procedure is chemical cleaning, a process designed to effectively clean process equipment and pipelines in a cost-effective …
حقوق النشر © 2024.Artom كل الحقوق محفوظة.خريطة الموقع