Jaw Crushers
Jaw crushers reduce large rocks or ore by means of compression. Mechanical pressure is applied using the crusher's two jaws; one is fixed while the other reciprocates. There are also primary and secondary …
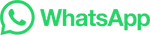
Jaw crushers reduce large rocks or ore by means of compression. Mechanical pressure is applied using the crusher's two jaws; one is fixed while the other reciprocates. There are also primary and secondary …
The JW Series jaw is designed for portability and ease of use. In addition, the rugged design provides the reliability that you can expect with products from ® Minerals Processing Systems. Reliability, quality, capacity, and ease of use—the ® JW Series jaw crushers are designed to help you be more profitable. That's what it's all ...
Our team is capable of fully repairing and maintaining aggregate equipment that includes crushers, screens, conveyors, tanks, and more. Our team has repaired and rebuilt …
Jaw-crusher Construction. Jaw crushers are heavy-duty machines and hence must be robustly constructed. The main frame is often made from cast iron or steel, connected with tie-bolts. It is commonly made in sections so that it can be transported underground for installation. Modern jaw crushers may have a main frame of welded mild steel plate.
The overarching principle guiding jaw crushers is a compression action. A V-shaped alignment houses the fixed jaw, serving as the immovable surface that facilitates the initial breakage. Simultaneously, the movable jaw, in a swinging motion, exerts force on the incoming material, compelling it against the unyielding surface of the fixed jaw.
Est. 1907. 100-199 Employees. Crusher including rock crushing equipment repairing & rebuilding services. Services include magnafluxing, sub-arc welding, stress relieving, grinding, welding, remachining & reassembling jaws, cones & impact/hammer mills. 24-hr service & repair available.
1,200 x 750 mm (47 x 29 in.) Max. feed size. 650 mm (26 in.) Capacity. 400 mtph (440 stph) QJ341 mobile jaw crusher is the ideal solution for a wide range of applications. Equipped with a C12 jaw crusher, a powerful and fuel-efficient engine, it is designed to tackle the most difficult operations. QJ341.
Heavy duty Coal Crushers are suited for the challenging opencast mining conditions. Jaw Crushers built for the high-impact conditions of the Ferrochrome industry. ... Our reputation is built on consistently and repeatedly repairing crushers fast and efficiently, with the highest standards and in the best possible lead times. ...
Rock Crusher & Screen Repairs / Rebuilds. Specializing in the mining and construction industries, Denver Machine Shop offers crusher and screen repair services. Repairing and rebuilding full machines as well as all components, we utilize a full machine shop, featuring a 120 in. lathe, 4-axis milling up to 90 x 72 in., a 600 ton press, key seater, honing, …
Repair Services: Provides timely and efficient repair services, including emergency repairs, to minimize downtime and restore functionality. Parts and Components: Maintains a well …
Stationary jaw crushers. jaw crushers are reliable, high-performing crushers built to optimize primary crushing applications in mines and quarries. These tough crushers are delivered with everything you need for plug-and-play installation and safety features to keep operators out of danger. Backed up with a complete Reliability and ...
Jaw crushers are commonly used as both primary and . secondary crushers [8]. Donovan [9] noted that th ere are . ... and flywheel is avoided when repairing or replac ing the . bearing; ...
By Carol Wasson and PQ Staff | February 1, 2014. A lot can be saved or achieved by giving your machine the attention it needs, including costs and time your crews could be spending elsewhere. With …
Jaw crushers, occasionally referred to as "toggle crushers," are the most common type of crusher. Material is compressed between a moving piece of steel and a stationary piece. Cone crushers are compression crushers that use a rotating piece of steel against a stationary piece of steel to reduce material. While similar in design and ...
Jaw crusher operation and maintenance. Jaw crushers are generally installed on top of the concrete foundations. Take into consideration of the weight of jaw crusher, the tough working conditions and the high inertia forces generated by the machine during operation, which may cause the slight vibration of foundation and machine system; therefore, the …
All jaw crushers reduce large sized rocks, ore, or other material by a compression action. A fixed jaw, mounted in a V-shaped alignment, is the stationary breaking surface, while a movable, "swing" jaw exerts force on …
1:59. McLanahan Universal Jaw Crushers are overhead eccentric jaw crushers that continuously reduce material as it passes through the crushing chamber with its aggressive force feed action as the movable jaw compresses inward and downward. The sharp primary blow at the top of the chamber reduces material instantly, while a secondary crushing ...
4. The relative position of the teeth groove of the moving jaw and the fixed jaw is wrong; 5. The voltage is too low; 6. The clearance between the movable jaw and the fixed jaw is too large, resulting in the rotation of the outer ring of the bearing. Solution: 1. Replace with a new crusher of appropriate model; 2.
Jaw crushers often come equipped with an adjustment mechanism that allows for the regulation of the crusher's closed side setting. This feature influences the final product size and overall ...
All jaw crushers reduce large sized rocks ore, or other materials by a compression action. A fixed jaw, mounted in a V-shaped alignment, is the stationary breaking surface, while a movable ...
Oversized Shaft, Dynamically Balanced Flywheels. All Lippmann heavy-duty jaw crushers feature an oversized, heat treated shaft forged of special alloy to provide an exceptionally large eccentric throw. These heavy-duty shafts are paired with two dynamically balanced flywheels, effectively reducing vibration on both portable and stationary crushers.
reinforced design of swing jaw to take up peak loads. crushing jaws can expand freely. compact and reliable design. quick and easy exchange of wear parts. easy adjustment of crushing gap. thyssenkrupp jaw crusher - Experience the next frontier of engineering jaw crushers guided by thyssenkrupp Polysius's solutions and services.
The main content of minor repairs includes checking and repairing the jaw break adjustment device, the clearance of the high-speed discharge port, and the adjustment or replacement of worn linings. Overhaul the transmission part, lubrication system, and replace the lubricating oil. The period of minor repairs is about 1-3 months.
Advantages of a Jaw Crusher. Many factors make laboratory jaw crushers the optimum selection for effective and efficient primary crushing of hard, brittle, rock-like materials. Laboratory models are available with sample top sizes from 0.75in to 8in (20mm to 203mm). Jaw plates are available in a variety of material types to optimize performance ...
Home. Concrete. 5 Common Questions about Jaw Crushers Answered. There are many types and styles of crushing equipment. Kemper Equipment explains how to choose the right crusher …
Problem 1: Broken toggle plate. A broken toggle plate is a serious problem that requires immediate attention. The first step is to shut down the jaw crusher and ensure that all power sources are disconnected. Once the machine is safe to work on, the broken toggle plate should be removed. Depending on the design of the jaw crusher, this may ...
Jaw Crushers. Available in a variety of sizes and configurations, the Hydra-Jaw® crusher, Pioneer® jaw crusher and Iron Giant jaw crushers deliver high-capacity crushing and reliable performance for increased operational productivity and profitability. Our diverse line of industry-leading jaw crushers offers producers the latest in jaw ...
Jaw crushers are used as primary crushers, or the first step in the process of reducing rock. They crush primarily by using compression. The rock is dropped between two rigid pieces of metal, one of which then moves inwards towards the rock, and the rock is crushed because it has a lower breaking point than the opposing metal piece.
Reversible jaw plates extend service life and the stationary jaw lifts easily from the frame for cleaning the inner parts. Sealed heavy bronze bearings are protected from dust and dirt, and lubricated by grease cups. Jaw size is 4x9in (102x229mm) with a 4x2.375in (102x60mm) opening. Reduction adjusts for 1/16–5/8in (1.6–15.9mm) particle size.
The overarching principle guiding jaw crushers is a compression action. A V-shaped alignment houses the fixed jaw, serving as the immovable surface that facilitates the …
حقوق النشر © 2024.Artom كل الحقوق محفوظة.خريطة الموقع